Introduction
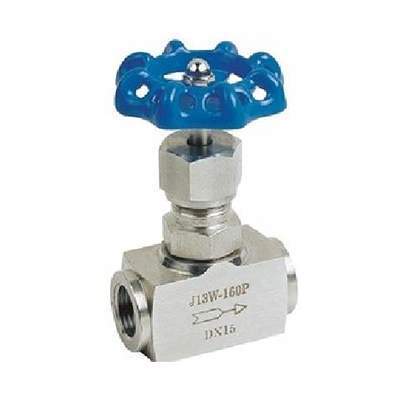
Threaded valves are indispensable components in a wide range of industrial and domestic applications, playing a critical role in controlling the flow of fluids and gases. From the intricate plumbing systems of modern homes to the complex pipelines of industrial facilities, threaded valves ensure the safe and efficient operation of countless processes. Selecting the appropriate threaded valve involves considering various factors, including its size and material. This comprehensive guide delves into the intricacies of threaded valve sizes and materials, empowering you to make informed decisions for your specific needs.
Threaded Valve Basics
A threaded valve comprises several key components: the body, the stem, and the packing. The body serves as the housing for the flow passage, while the stem, often equipped with a handle or wheel, controls the opening and closing of the valve. The packing, typically a resilient material like PTFE or graphite, ensures a leak-proof seal between the stem and the body. Threaded valves are connected to pipes or fittings using male or female threads, which are standardized to facilitate compatibility and ease of installation.
Common Threaded Valve Types
Threaded valves come in various types, each designed for specific applications and flow control requirements. Some of the most common types include:
- Ball Valve: Known for its quarter-turn operation, the ball valve offers rapid on/off control. It consists of a spherical ball with a hole drilled through its center. By rotating the handle, the ball aligns or obstructs the flow passage.
- Gate Valve: Ideal for applications requiring precise flow regulation, the gate valve features a movable gate that slides perpendicular to the flow direction. When fully open, the gate offers minimal resistance to flow.
- Globe Valve: Well-suited for throttling and shut-off applications, the globe valve utilizes a disc-shaped plug that moves up and down within the valve body. By adjusting the position of the plug, the flow can be controlled.
- Check Valve: Designed to prevent backflow, the check valve allows fluid to flow in only one direction. It typically employs a swinging disc or ball that automatically closes to block reverse flow.
- Butterfly Valve: Featuring a disc-shaped element that rotates within the valve body, the butterfly valve provides efficient flow control. It is commonly used in large-diameter pipelines due to its compact design and ease of operation.
Threaded Valve Sizes
Threaded valve sizes are typically denoted by their nominal diameter, expressed in inches or millimeters. The nominal diameter refers to the approximate inside diameter of the pipe or fitting to which the valve is connected. However, it is essential to note that the actual internal diameter of the valve may vary slightly. Other crucial dimensions to consider include the thread pitch, which determines the number of threads per inch, and the thread profile, which defines the shape of the thread.
Threaded Valve Materials
The material of a threaded valve plays a pivotal role in determining its performance, durability, and compatibility with various fluids. The choice of material depends on factors such as the fluid’s properties, the operating temperature and pressure, and the desired level of corrosion resistance. Common materials used in threaded valve construction include:
- Brass: Renowned for its excellent corrosion resistance, brass is commonly used in low-pressure applications involving water and gas. It offers good machinability and is relatively easy to work with.
- Stainless Steel: Highly resistant to corrosion, stainless steel is ideal for applications involving aggressive chemicals and high-temperature fluids. It is available in various grades, each offering specific properties and benefits.
- Cast Iron: Durable and cost-effective, cast iron is often used in heavy-duty applications. However, it is susceptible to corrosion, particularly in wet environments.
- Plastic: Lightweight and corrosion-resistant, plastic valves are suitable for low-pressure applications involving non-aggressive fluids. They are often used in domestic plumbing and irrigation systems.
Factors Affecting Threaded Valve Selection
Several factors must be considered when selecting a threaded valve to ensure optimal performance and longevity:
- Fluid Compatibility: The valve material must be compatible with the fluid being handled to prevent corrosion, degradation, and potential contamination.
- Pressure Rating: The valve’s pressure rating should exceed the maximum operating pressure to avoid catastrophic failure.
- Temperature Rating: The valve’s temperature rating must accommodate the fluid’s temperature range to prevent thermal stress and material degradation.
- Flow Rate: The valve must be adequately sized to handle the required flow rate without causing excessive pressure drop or turbulence.
- End Connections: The valve’s end connections, whether male or female threads, must be compatible with the pipe or fitting to ensure a secure and leak-proof joint.
Threaded Valve Standards
To ensure interchangeability and quality control, threaded valves are manufactured according to various industry standards. Some of the most common standards include:
- National Pipe Thread (NPT): A U.S. standard widely used in North America.
- British Standard Pipe Thread (BSPT): A British standard commonly used worldwide.
- Metric Parallel Thread (MPT): A metric standard used in many countries.
Adherence to these standards guarantees that threaded valves from different manufacturers can be easily interchanged, simplifying maintenance and repair tasks.
Threaded Valve Installation
Proper installation is crucial to ensure the reliable and efficient operation of a threaded valve. The following steps outline the general procedure for installing a threaded valve:
- Clean the Threads: Remove any dirt, debris, or old sealant from the threads of the valve and the pipe or fitting.
- Apply Thread Sealant: Apply a suitable thread sealant, such as Teflon tape or pipe dope, to the male threads to prevent leaks.
- Hand-Tighten the Valve: Hand-tighten the valve onto the pipe or fitting, ensuring a snug fit without excessive force.
- Use a Wrench for Final Tightening: Use a wrench to tighten the valve to the manufacturer’s specified torque, ensuring a secure and leak-proof connection.
Threaded Valve Maintenance
Regular maintenance is essential to prolong the life of a threaded valve and prevent potential issues. The following maintenance practices should be followed:
- Inspect for Leaks: Periodically inspect the valve and its connections for any signs of leaks. Tighten loose connections or replace damaged gaskets or packing as needed.
- Lubricate Moving Parts: Lubricate the valve stem and other moving parts with a suitable lubricant to reduce friction and ensure smooth operation.
- Clean the Valve: Clean the valve body and stem to remove any debris or buildup that may hinder performance.
- Replace Worn Parts: Replace any worn or damaged components, such as the packing or stem, to restore the valve’s functionality.
Threaded Valve Sizing Chart
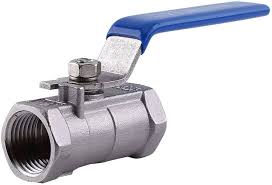
Nominal Diameter (inches) | Thread Size (NPT) | Common Applications |
---|---|---|
1/4 | 1/4 NPT | Small-scale plumbing, instrumentation |
1/2 | 1/2 NPT | General plumbing, gas lines |
3/4 | 3/4 NPT | Water supply, HVAC systems |
1 | 1 NPT | Larger plumbing systems, industrial applications |
1-1/4 | 1-1/4 NPT | Industrial piping, process equipment |
1-1/2 | 1-1/2 NPT | Heavy-duty industrial applications |
Conclusion
By understanding the intricacies of threaded valve sizes and materials, you can make informed decisions to select the optimal valve for your specific application. Consider factors such as fluid compatibility, pressure and temperature ratings, flow rate, and end connections to ensure reliable and efficient performance. Adhering to proper installation and maintenance practices will further extend the life of your threaded valves.
FAQ
What is the difference between NPT and BSPT threads?
NPT threads have a 60-degree included angle, while BSPT threads have a 55-degree included angle.
How do I convert inches to millimeters for threaded valves?
Use a conversion factor of 25.4 millimeters per inch.
Can I use a Teflon tape on all threaded connections?
While Teflon tape is suitable for many applications, it may not be suitable for high-pressure or high-temperature applications.