Welcome to My Blog!
Before we dive into the content, I’d love for you to join me on my social media platforms where I share more insights, engage with the community, and post updates. Here’s how you can connect with me:
Facebook: https://www.facebook.com/profile.php?id=61563865935136
Now, let’s get started on our journey together. I hope you find the content here insightful, engaging, and valuable.
Introduction
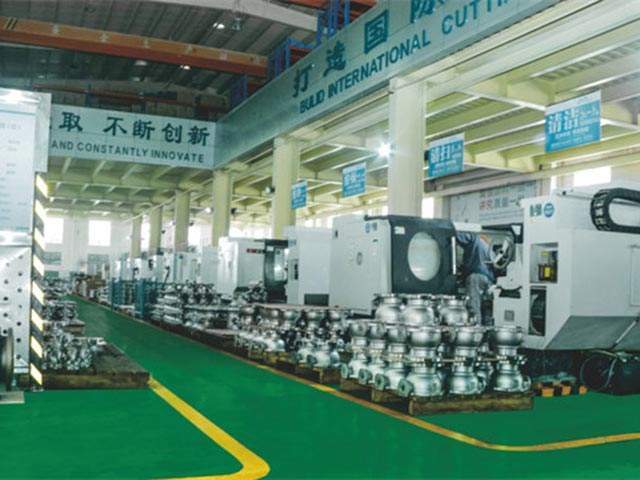
Butterfly valves are essential components in fluid flow systems, offering reliable control and regulation. Known for their compact design and ease of operation, these valves are used across various industries, including water treatment, chemical processing, and oil and gas. With several butterfly valve types available, understanding their unique features and applications is crucial for selecting the right one for your system.
This article provides an in-depth exploration of different butterfly valve types, their working principles, and factors to consider when choosing the most suitable option. By gaining a comprehensive understanding, you can enhance system efficiency, reduce maintenance costs, and ensure optimal performance.
What Are Butterfly Valves?
Overview of Butterfly Valves
Butterfly valves are quarter-turn rotational valves used to control fluid flow. They feature a disc that rotates around an axis to open or close the valve. When the disc is parallel to the flow, the valve is open, and when perpendicular, it is closed.
Key Components of a Butterfly Valve:
- Body: The main framework that houses the valve’s internal components.
- Disc: The central element that regulates the flow.
- Stem: Connects the disc to the actuator or handle.
- Seat: Ensures a tight seal when the valve is closed.
- Actuator: Operates the valve, which can be manual, pneumatic, or electric.
Different Types of Butterfly Valves
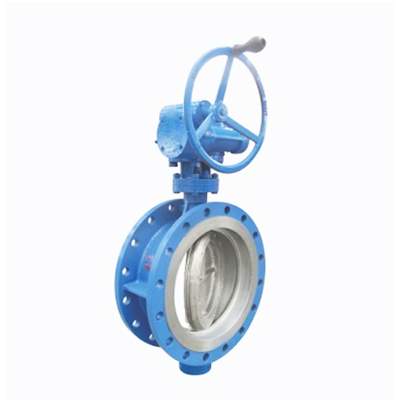
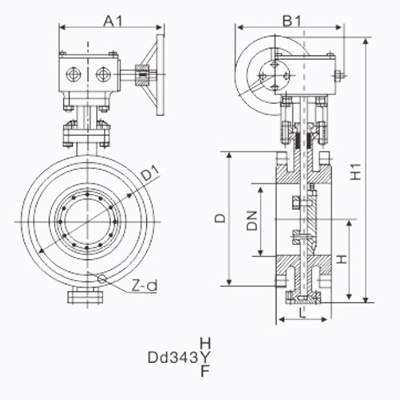
1. Wafer Butterfly Valve
The wafer butterfly valve is the most common type, designed to fit between two flanges. It uses seals on both sides to prevent backflow, making it ideal for applications requiring bidirectional flow.
Applications:
- Water distribution systems
- HVAC systems
- Food processing
2. Lug Butterfly Valve
The lug butterfly valve has threaded inserts, allowing it to be bolted to flanges on both sides. This design permits one side to be disconnected without affecting the other, making maintenance more convenient.
Applications:
- Chemical processing
- Marine systems
- Power generation
3. Double Offset Butterfly Valve
Also known as high-performance butterfly valves, these feature two offsets from the disc’s axis. This design reduces wear and improves sealing performance, making them suitable for high-pressure and high-temperature environments.
Applications:
- Oil and gas pipelines
- Petrochemical plants
- Power plants
4. Triple Offset Butterfly Valve
The triple offset butterfly valve incorporates an additional offset, enhancing its sealing capabilities. It is commonly used in critical applications requiring zero leakage and superior durability.
Applications:
- Cryogenic services
- Steam systems
- Corrosive environments
5. Rubber-Lined Butterfly Valve
This type features a rubber lining on the seat, offering excellent corrosion resistance and flexibility. It is primarily used in low-pressure applications.
Applications:
- Wastewater treatment
- Mining
- Agricultural irrigation
Comparison of Butterfly Valve Types
The table below highlights the key differences between various butterfly valve types to help you make an informed decision:
Type | Design Feature | Common Applications | Advantages |
---|---|---|---|
Wafer Butterfly Valve | Compact design, fits between flanges | Water systems, HVAC | Lightweight, easy installation |
Lug Butterfly Valve | Threaded inserts for easy disconnection | Chemical processing, marine systems | Easy maintenance, bidirectional flow |
Double Offset Valve | Two offsets for reduced wear | Oil pipelines, power plants | High durability, excellent sealing |
Triple Offset Valve | Three offsets for zero leakage | Steam, cryogenic services | Superior performance, no leakage |
Rubber-Lined Valve | Rubber seat for corrosion resistance | Wastewater, agriculture | Cost-effective, corrosion-resistant |
Key Factors to Consider When Choosing Butterfly Valve Types
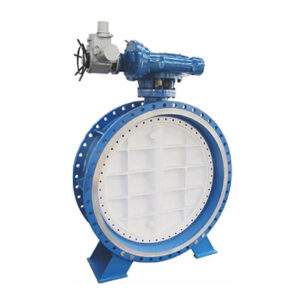
1. Application Requirements
Understand the fluid type, pressure, temperature, and flow rate to determine the valve’s compatibility.
2. Material Selection
Choose materials that can withstand the operating conditions. For example, stainless steel is ideal for corrosive environments, while rubber-lined valves are suitable for low-pressure systems.
3. Maintenance Needs
Some butterfly valve types, like lug valves, offer easier maintenance options, which can reduce downtime and costs.
4. Operating Mechanism
Decide between manual, pneumatic, or electric actuation based on your system’s automation level.
5. Cost and Budget
While initial cost is important, consider long-term expenses such as maintenance and replacement when making your decision.
The Advantages of Butterfly Valves
Butterfly valves are favored in industrial applications due to their many benefits:
- Compact Design: Saves space in confined areas.
- Ease of Operation: Requires minimal torque to open and close.
- Cost-Effectiveness: More affordable than other valve types.
- Versatility: Suitable for a wide range of fluids, including gases and liquids.
- Durability: Long-lasting with proper maintenance.
Conclusion
Understanding the various butterfly valve types is essential for optimizing your fluid control system. Each type has unique features, advantages, and applications, making it crucial to evaluate your system requirements before making a selection. Whether you need a basic wafer valve for water distribution or a high-performance triple offset valve for steam systems, choosing the right butterfly valve enhances efficiency, reliability, and performance.
FAQ
How do I determine which butterfly valve type is best for my system?
Consider factors like fluid type, pressure, temperature, and required sealing performance. Consulting with a professional or valve manufacturer can also help.
What is the main difference between a double offset and a triple offset butterfly valve?
A double offset valve has two offsets for reduced wear and better sealing, while a triple offset valve adds an additional offset to ensure zero leakage in critical applications.
Can butterfly valves handle high-pressure systems?
Yes, certain types like double offset and triple offset butterfly valves are designed for high-pressure applications.
Are butterfly valves suitable for corrosive environments?
Yes, rubber-lined and triple offset butterfly valves are commonly used in corrosive environments due to their material resistance and sealing capabilities.
What maintenance is required for butterfly valves?
Regular inspection, cleaning, and lubrication of moving parts are essential for ensuring long-term performance. Additionally, replacing worn-out components like seals and seats helps maintain efficiency.
Can butterfly valves be automated?
Yes, butterfly valves can be automated with pneumatic, electric, or hydraulic actuators, depending on the system’s requirements.
Why are triple offset butterfly valves used in cryogenic applications?
Triple offset valves provide zero leakage and can withstand extreme temperatures, making them ideal for cryogenic services.