Introduction
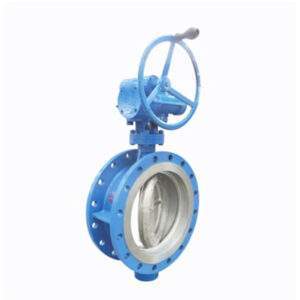
Butterfly valves are indispensable components in a wide range of industries, from oil and gas to water treatment. They offer a simple yet efficient solution for controlling fluid flow. The material composition of a butterfly valve is a critical factor that significantly influences its performance, durability, and suitability for specific applications. In this comprehensive guide, we will delve into the diverse materials used in butterfly valves, their unique properties, and their ideal applications.
The Anatomy of a Butterfly Valve
A butterfly valve comprises several key components:
- Body: The main housing that encloses the valve’s internal mechanisms.
- Disc: A circular plate that rotates to control fluid flow.
- Stem: The shaft that connects the disc to the actuator.
- Seat: The sealing surface against which the disc presses to prevent leakage.
The material selection for each component, particularly the disc and body, is crucial in determining the valve’s overall performance and longevity.
Why Material Matters
The choice of material for a butterfly valve is influenced by several factors:
- Fluid Properties: The corrosiveness, temperature, and pressure of the fluid being controlled.
- Operating Conditions: The valve’s exposure to extreme temperatures, abrasive particles, and frequent cycling.
- Regulatory Compliance: Adherence to industry standards and regulations.
- Cost-Effectiveness: The initial purchase price and long-term maintenance costs.
Common Materials Used in Butterfly Valves
Cast Iron
- Advantages: Cost-effective, good mechanical strength.
- Disadvantages: Susceptible to corrosion, limited temperature range.
- Applications: Low-pressure water and air services, non-corrosive fluids.
Cast iron butterfly valves are a budget-friendly option for applications involving low-pressure, non-corrosive fluids. However, their limited corrosion resistance and temperature range restrict their use in more demanding environments.
Ductile Iron
- Advantages: Improved corrosion resistance compared to cast iron, higher tensile strength.
- Disadvantages: Can still corrode in aggressive environments.
- Applications: Water, wastewater, and mildly corrosive services.
Ductile iron offers enhanced properties over cast iron, making it suitable for a wider range of applications, including water, wastewater, and mildly corrosive services.
Stainless Steel
- Advantages: Excellent corrosion resistance, high strength, wide temperature range.
- Disadvantages: Higher cost compared to other materials.
- Applications: Chemical processing, food and beverage, pharmaceutical industries.
Stainless steel is a premium material choice for butterfly valves, offering exceptional corrosion resistance, high strength, and the ability to withstand a wide range of temperatures. It is ideal for demanding applications in industries like chemical processing, food and beverage, and pharmaceuticals.
Carbon Steel
- Advantages: High strength, good weldability, cost-effective.
- Disadvantages: Susceptible to corrosion, requires coatings or linings for corrosive environments.
- Applications: High-temperature and high-pressure applications where corrosion is not a major concern.
Carbon steel is a strong and cost-effective material, but its susceptibility to corrosion limits its use in certain applications. It is often employed in high-temperature and high-pressure environments where corrosion is not a primary concern.
Non-Metallic Materials
- Advantages: Lightweight, corrosion-resistant, suitable for abrasive fluids.
- Disadvantages: Lower temperature and pressure limits compared to metals.
- Applications: Food processing, chemical processing, and abrasive slurry services.
Non-metallic materials like PVC, PTFE, and polypropylene offer excellent corrosion resistance and are lightweight, making them suitable for specific applications, particularly in the food processing, chemical processing, and abrasive slurry industries.
Material Comparison Table
Material | Corrosion Resistance | Temperature Range | Pressure Rating | Applications |
---|---|---|---|---|
Cast Iron | Low | Moderate | Low to medium | Water, air, non-corrosive fluids |
Ductile Iron | Moderate | Moderate | Medium | Water, wastewater, mildly corrosive services |
Stainless Steel | Excellent | Wide | High | Chemical processing, food, pharmaceutical |
Carbon Steel | Low | High | High | High-temperature, high-pressure applications |
Non-Metallic | Excellent | Moderate | Low to medium | Food processing, chemical processing, abrasive slurries |
Factors Affecting Material Selection
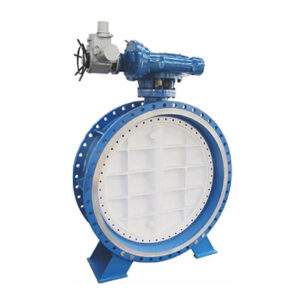
- Fluid Compatibility: The material must be resistant to the chemical composition of the fluid to prevent corrosion and contamination.
- Operating Temperature: The material should be able to withstand the temperature extremes of the operating environment without compromising its mechanical properties.
- Pressure Rating: The material must be capable of handling the maximum pressure the valve will encounter.
- Abrasion Resistance: For applications involving abrasive fluids, the material should possess good abrasion resistance to prevent premature wear.
- Cycle Life: The material must be durable enough to withstand repeated cycles of opening and closing.
Conclusion
The selection of the appropriate material for a butterfly valve is a crucial decision that directly impacts its performance, reliability, and lifespan. By carefully considering the factors discussed in this guide, engineers and specifiers can make informed choices to ensure optimal valve performance in various industrial applications.
FAQ
What is the most common material for butterfly valves?
Stainless steel and carbon steel are among the most common materials due to their versatility and cost-effectiveness.
How do I choose the right material for my application?
Consider the fluid properties, operating conditions, and regulatory requirements. Consult with a valve specialist for assistance.
Can butterfly valves be made from plastic?
Yes, non-metallic materials like PVC, PTFE, and polypropylene are often used for butterfly valves in specific applications.