Introduction
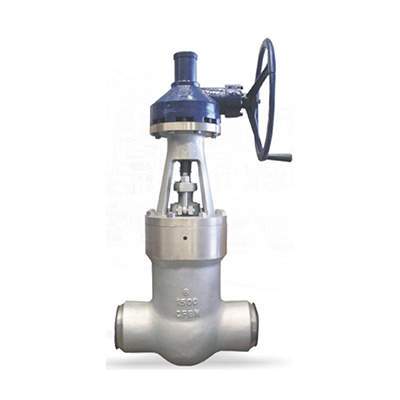
Power station valves are critical components in the intricate machinery of power generation facilities. These specialized valves are meticulously engineered to control the flow of various fluids, including steam, water, and gases, within the power plant. From the delicate regulation of pressure to the robust prevention of leaks and the isolation of equipment, power station valves play an indispensable role in ensuring the overall safety and reliability of the power plant.
Understanding Power Station Valves
Power station valves are categorized based on their specific function, construction, and the nature of the medium they are designed to control. Some of the most common types of power station valves include:
- Gate valves: These valves are primarily employed for the on-off control of fluid flow. They are characterized by a gate-like disk that moves perpendicularly to the flow direction, effectively blocking or allowing the passage of fluid.
- Globe valves: Ideal for applications requiring precise throttling, globe valves utilize a spherical plug that moves up and down within the valve body, enabling fine-tuned control over the flow rate.
- Ball valves: Offering swift and decisive shut-off capabilities, ball valves are commonly used for isolation purposes. They feature a spherical ball with a bore through its center, which rotates to either obstruct or permit fluid flow.
- Butterfly valves: These valves are well-suited for large-diameter pipelines and provide efficient flow control. They consist of a disk-shaped element that rotates within the valve body, regulating the flow by varying the degree of opening.
- Check valves: Designed to prevent the backflow of fluids, check valves ensure unidirectional flow. They automatically open in the direction of forward flow and close when the flow reverses.
- Safety valves: These essential valves safeguard equipment from potentially damaging overpressure conditions. They are designed to automatically relieve excess pressure by opening when a predetermined pressure threshold is exceeded.
The Importance of Valve Selection
The judicious selection of power station valves is paramount to ensuring optimal performance and safety. Several key factors must be carefully considered during the valve selection process:
- Operating conditions: The temperature, pressure, and corrosive properties of the fluid to be controlled significantly influence the choice of valve material and design.
- Flow requirements: The required flow capacity and velocity of the fluid dictate the valve’s size and flow coefficient.
- Actuation: The desired method of valve operation, whether manual, pneumatic, or electric, must be carefully considered.
- Material compatibility: The valve materials must be compatible with the fluid to prevent corrosion, erosion, and other forms of degradation.
Valve Maintenance and Inspection
A robust maintenance and inspection program is essential to prolong the lifespan and ensure the reliable operation of power station valves. Key maintenance activities include:
- Visual inspection: Regular visual inspections help identify signs of wear, corrosion, or damage to the valve body, stem, and other components.
- Leak testing: Periodic leak testing is crucial to detect and address any leaks that may compromise safety and efficiency.
- Lubrication: Proper lubrication of moving parts, such as the valve stem and packing, reduces friction and prevents premature wear.
- Calibration: Calibration ensures that the valve operates accurately and consistently within specified tolerances.
The Role of Valves in Emergency Shutdown
Power station valves play a critical role in executing emergency shutdown procedures. In the event of a system failure or hazardous condition, valves can be rapidly activated to isolate equipment and prevent the escalation of the incident. This rapid isolation helps to contain the problem, minimize damage, and safeguard personnel.
Safety Features of Power Station Valves
Modern power station valves are equipped with various safety features designed to enhance their reliability and minimize the risk of accidents:
- Dual block and bleed: This safety feature provides an additional layer of protection by isolating a valve from the system, ensuring that it can be safely maintained or repaired.
- Lockout/tagout procedures: These procedures help prevent accidental operation of valves during maintenance or repair activities, safeguarding personnel and equipment.
- Pressure relief devices: These devices, such as safety relief valves, are integrated into the valve design to protect the valve itself from overpressure conditions.
Common Valve-Related Issues and Solutions
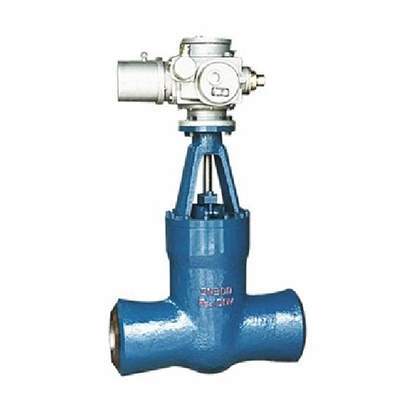
Issue | Cause | Solution |
---|---|---|
Valve leakage | Worn or damaged seals, improper installation, corrosion | Replace seals, re-torque connections, inspect for corrosion |
Valve sticking | Build-up of deposits, lack of lubrication, misalignment | Clean the valve, lubricate moving parts, align the valve |
Valve cavitation | Excessive flow velocity, improper valve selection | Reduce flow velocity, select a valve with a larger flow coefficient |
Valve erosion | Abrasive particles in the fluid, improper valve selection | Install strainers, select a valve with erosion-resistant materials |
Conclusion
Power station valves are indispensable components of modern power generation facilities. By understanding their function, selection criteria, and maintenance requirements, operators can ensure the safe and reliable operation of their plants. Regular inspection, maintenance, and adherence to rigorous safety procedures are essential to prevent accidents, minimize downtime, and optimize the overall performance of the power plant.
FAQ
What is the difference between a gate valve and a globe valve?
Gate valves are primarily used for on-off service, while globe valves are better suited for throttling applications.
How often should power station valves be inspected?
The frequency of inspection depends on factors such as the valve’s operating conditions and criticality. A detailed inspection schedule should be developed based on the manufacturer’s recommendations and industry best practices.
What are the safety implications of a leaking valve?
Valve leakage can lead to loss of containment, environmental damage, and increased maintenance costs. In severe cases, it can pose a safety hazard to personnel.