Introduction
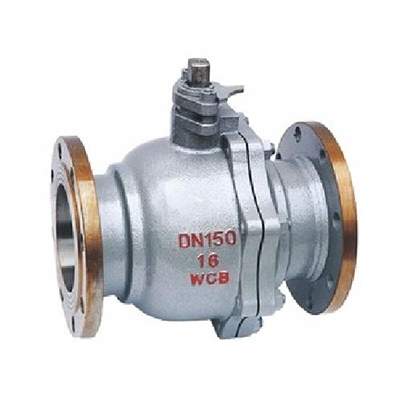
Floating ball valves have emerged as a prominent solution for controlling fluid flow across diverse industrial sectors. Their design, characterized by a buoyant spherical element within the valve body, offers a compelling blend of simplicity, efficiency, and reliability. This comprehensive guide will delve into the multifaceted advantages of incorporating floating ball valves, explore their diverse applications, and address common inquiries regarding their functionality and selection. We will examine how these valves function, analyze their key strengths, and investigate their suitability across various industries, ultimately providing a comprehensive understanding of their significance in modern fluid handling systems.
How Does a Floating Ball Valve Work?
At the core of a floating ball valve lies a straightforward yet ingenious mechanism. The valve body serves as the housing, encompassing a spherical ball that possesses the freedom to move within its confines. This movement is precisely regulated by a stem, which acts as the control element. In the open position, the stem elevates the ball, effectively disengaging it from the valve seat, thereby permitting unimpeded fluid flow. Conversely, when the valve is closed, the stem lowers the ball, forcing it into firm contact with the seat, creating a secure and leak-proof seal. The inherent buoyancy of the ball ensures its stable positioning, minimizing the impact of fluctuating flow conditions and maintaining consistent performance.
Advantages of Using a Floating Ball Valve
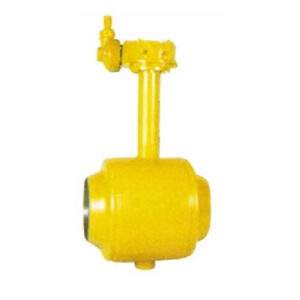
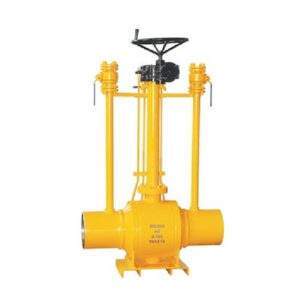
Unwavering Reliability and Exceptional Durability
Floating ball valves are renowned for their exceptional reliability and remarkable durability. The inherent simplicity of their design, coupled with robust construction, contributes significantly to their longevity. The absence of intricate internal components minimizes the potential for wear and tear, reducing the likelihood of malfunctions and ensuring consistent performance over extended periods. This inherent robustness translates to reduced maintenance requirements and enhanced operational efficiency, making them a cost-effective and dependable solution for various fluid handling applications.
Uncompromising Sealing Integrity
A hallmark feature of floating ball valves is their ability to establish a remarkably tight seal. The spherical geometry of the ball provides an expansive and uniformly smooth sealing surface, ensuring effective contact with the valve seat even under demanding conditions, such as elevated pressures. This exceptional sealing capability is critical in applications where the prevention of leaks is paramount, such as those involving hazardous or valuable fluids. By minimizing leakage, floating ball valves contribute to enhanced safety, reduced environmental impact, and improved operational efficiency.
Effortless and Intuitive Operation
Operating a floating ball valve is an intuitive and straightforward process. A simple quarter-turn of the valve stem suffices to transition between the fully open and fully closed positions. This ease of operation makes them highly adaptable to both manual and automated control systems. The streamlined operational characteristics contribute to increased efficiency, reduced operator training requirements, and enhanced overall system control.
Versatility and Adaptability
The versatility of floating ball valves is a testament to their design. These valves can be effectively employed across a diverse spectrum of applications, encompassing:
- Water Treatment: Controlling the flow of water within filtration and purification systems, ensuring precise regulation of treatment processes.
- Chemical Processing: Handling corrosive and hazardous fluids with confidence, providing reliable isolation and control within demanding chemical environments.
- Oil and Gas: Managing the flow of hydrocarbons within pipelines and refineries, facilitating efficient and safe operations within the energy sector.
- Food and Beverage: Ensuring the purity and safety of food and beverage products by controlling the flow of liquids and gases within processing and packaging lines.
This broad applicability underscores the adaptability and value of floating ball valves in modern industrial settings.
Minimal Maintenance Requirements
One of the significant advantages of floating ball valves is their low maintenance demands. The limited number of moving parts within the valve assembly minimizes the potential for wear and tear, reducing the frequency and complexity of maintenance interventions. This translates to reduced downtime, lower maintenance costs, and improved overall operational efficiency.
Compact and Space-Saving Design
The compact and streamlined design of floating ball valves facilitates their integration into confined spaces. Their relatively small footprint minimizes installation challenges and maximizes space utilization within existing systems. This space-saving characteristic is particularly valuable in applications where space constraints are a critical consideration.
Cost-Effectiveness and Value Proposition
Despite their numerous advantages, including reliability, durability, and versatility, floating ball valves are generally considered cost-effective solutions. Their competitive pricing, coupled with their long service life and minimal maintenance requirements, makes them a compelling value proposition for a wide range of applications.
Comparison of Floating Ball Valves and Other Valve Types
Feature | Floating Ball Valve | Gate Valve | Globe Valve |
---|---|---|---|
Sealing Mechanism | Spherical ball provides a wide sealing surface, ensuring a tight seal. | Wedge-shaped gate creates a linear seal, potentially susceptible to leakage. | Disc-shaped plug provides a circular sealing surface, but can be prone to wear and tear. |
Operation | Quarter-turn operation for quick and efficient control. | Linear motion requires more effort and time to open or close. | Linear motion, similar to globe valves, can require significant effort for operation. |
Flow Control | Suitable for both on/off and throttling applications, offering versatility in flow control. | Primarily designed for on/off applications, with limited throttling capabilities. | Well-suited for throttling applications, providing precise control over flow rates. |
Maintenance | Low maintenance requirements due to simple design and robust construction. | Moderate maintenance demands, requiring periodic inspection and lubrication. | Higher maintenance requirements due to potential for wear and tear on the valve seat and plug. |
Cost | Generally cost-effective compared to other valve types, offering a favorable return on investment. | Typically higher in cost compared to ball valves, especially for larger sizes. | Can be more expensive than ball valves, particularly for high-pressure applications. |
Applications of Floating Ball Valves
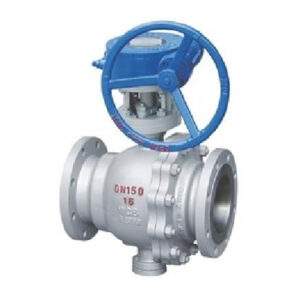
The versatility of floating ball valves has led to their widespread adoption across a broad spectrum of industries. Some of the most prominent application areas include:
- Plumbing Systems: Controlling the flow of water to fixtures and appliances within residential and commercial buildings, ensuring efficient and reliable water distribution.
- Irrigation Systems: Regulating the flow of water to crops, optimizing water usage and maximizing agricultural productivity.
- HVAC Systems: Controlling the flow of air and water within heating, ventilation, and air conditioning systems, ensuring optimal performance and energy efficiency.
- Industrial Processes: Handling a wide range of fluids, including chemicals, gases, and slurries, within various industrial processes, facilitating efficient and safe operations.
These diverse applications underscore the critical role of floating ball valves in modern industrial and infrastructure systems.
Conclusion
Floating ball valves have established themselves as indispensable components within a wide range of industrial and infrastructure systems. Their inherent advantages, including reliability, durability, versatility, and cost-effectiveness, make them a preferred choice for numerous fluid handling applications. By understanding the principles of operation, exploring the diverse advantages, and considering the critical factors involved in selection and application, engineers and technicians can effectively leverage the benefits of floating ball valves to optimize system performance, enhance efficiency, and ensure safe and reliable operations.
FAQ
What is the difference between a floating ball valve and a trunnion ball valve?
While both types utilize a spherical ball for sealing, trunnion ball valves incorporate a trunnion or bearing system to support the ball, enhancing their suitability for high-pressure applications. Floating ball valves, on the other hand, rely on the buoyancy of the ball for support, making them more suitable for lower pressure applications.
How do I select the right size of floating ball valve for my application?
The selection of the appropriate size of floating ball valve is crucial for optimal performance. Key factors to consider include the required flow rate, the operating pressure and temperature, and the type of fluid being handled. Consulting engineering guidelines and manufacturer specifications is essential for making an informed decision.
What materials are floating ball valves made of?
Floating ball valves are typically manufactured from a variety of materials, including brass, stainless steel, and various types of plastics. The choice of material depends on the specific application and the properties of the fluid being handled, such as corrosiveness, temperature, and pressure.
How often should I replace the seals in a floating ball valve?
The frequency of seal replacement varies depending on factors such as the operating conditions, the type of fluid, and the material of the seals. Regular inspections and maintenance checks are recommended to assess the condition of the seals and determine the appropriate replacement schedule.
Can floating ball valves be used in high-temperature applications?
Yes, floating ball valves can be used in high-temperature applications, provided they are constructed from suitable materials, such as high-temperature alloys or specialized plastics. It is crucial to consult the manufacturer’s specifications to determine the maximum operating temperature for a specific valve model.