Welcome to My Blog!
Before we dive into the content, I’d love for you to join me on my social media platforms where I share more insights, engage with the community, and post updates. Here’s how you can connect with me:
Facebook:https://www.facebook.com/profile.php?id=61563865935136
Now, let’s get started on our journey together. I hope you find the content here insightful, engaging, and valuable.
Introduction
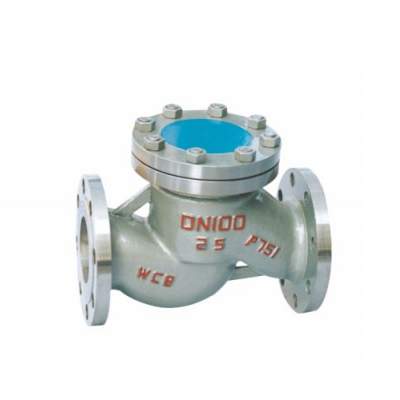
A stop check valve is an essential component in various fluid handling systems, designed to prevent backflow and also provide the capability to manually stop flow. Understanding the nuances of a stop check valve, including its applications and benefits, is crucial for selecting the right valve for specific needs. This guide delves into the key aspects of stop check valve functionality, its diverse uses, and the advantages it offers in industrial and commercial settings.
What is a Check Valve and How Does it Work?
A check valve combines the features of a check valve and a globe valve. The check valve portion automatically prevents backflow, while the globe valve functionality allows for manual shut-off. This dual functionality is achieved through a disc that can either swing freely to allow flow in one direction or be manually positioned to block flow entirely. This design ensures that the check valve provides both automatic backflow prevention and manual flow control.
Key Differences: Stop Check Valve vs. Traditional Check Valve
While both stop check valves and traditional check valves prevent backflow, the fundamental difference lies in the manual shut-off capability. Traditional check valves, such as swing check valves or lift check valves, operate solely on fluid pressure, allowing flow in one direction and automatically closing to prevent reverse flow. A check valve, however, adds a manual override feature, providing greater control and flexibility in fluid handling systems.
The Diverse Applications of a Stop Check Valve
The versatility of a check valve makes it suitable for a wide range of applications. These include:
- Boiler Feedwater Systems: In boiler systems, check valves prevent backflow of high-pressure water, ensuring efficient and safe operation.
- Power Generation: Power plants utilize check valves to control the flow of steam and other fluids, maintaining system integrity.
- Chemical Processing: In chemical plants, these valves handle corrosive and hazardous fluids, providing both backflow prevention and manual shut-off for maintenance and safety.
- Oil and Gas Industry: Stop check valves are vital in pipelines and processing facilities, where they manage the flow of hydrocarbons and other fluids.
- Water Treatment: Water treatment plants use check valves to prevent contamination and maintain flow direction in various stages of the treatment process.
- HVAC Systems: Used in large scale heating and cooling systems to control fluid flow, and prevent backflow.
Benefits of Using a Stop Check Valve
Utilizing a stop check valve offers several significant benefits:
- Enhanced Safety: The ability to manually shut off flow provides an extra layer of safety during maintenance and emergencies.
- Improved System Control: The dual functionality allows for precise control of fluid flow, optimizing system performance.
- Reduced Maintenance: By preventing backflow, check valves minimize wear and tear on pumps and other equipment, reducing maintenance needs.
- Increased Efficiency: Ensuring unidirectional flow improves system efficiency and reduces energy consumption.
- Versatility: Suitable for a wide range of applications and fluids, making them a versatile choice for various industries.
Materials and Construction of High-Quality Stop Check Valves
The materials and construction of a stop check valve are critical to its performance and longevity. Common materials include:
- Carbon Steel: Suitable for general-purpose applications.
- Stainless Steel: Ideal for corrosive environments.
- Alloy Steel: Used in high-pressure and high-temperature applications.
- Cast Iron: Used in many water applications.
The construction typically involves a robust body, a disc that can swing or be positioned manually, and a seat that provides a tight seal. Proper material selection and construction ensure that the check valve can withstand the operating conditions and provide reliable performance.
Installation and Maintenance Best Practices for Check Valves
Proper installation and maintenance are essential for ensuring the longevity and optimal performance of a stop check valve. Key considerations include:
- Correct Orientation: Installing the valve in the correct flow direction is crucial.
- Proper Sealing: Ensuring a tight seal between the valve and the piping system prevents leaks.
- Regular Inspections: Periodic inspections and maintenance are necessary to identify and address any issues.
- Lubrication: Certain types of check valves require lubrication on their moving parts.
Understanding Pressure and Temperature Ratings for Check Valves
Pressure and temperature ratings are critical factors to consider when selecting a check valve. These ratings determine the maximum pressure and temperature the valve can handle without failure. Exceeding these ratings can lead to valve damage and system failure. It’s essential to select a check valve with ratings that meet or exceed the operating conditions of the system.
Stop Check Valve Selection Considerations
When choosing a check valve, consider the following factors:
- Fluid Type: The type of fluid being handled will determine the appropriate valve material.
- Operating Pressure and Temperature: The valve must be rated for the operating conditions of the system.
- Size and Connection Type: The valve size and connection type must match the piping system.
- Application requirements: the specific needs of the system where the valve will be installed.
Stop Check Valve Specifications Table
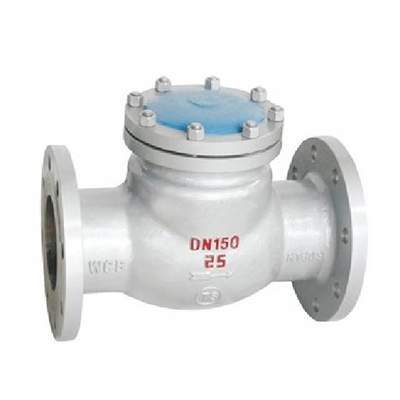
Specification | Description |
---|---|
Valve Type | Stop Check Valve |
Material | Carbon Steel, Stainless Steel, Alloy Steel, Cast Iron |
Size Range | 1/2 inch to 24 inches |
Pressure Rating | ANSI Class 150 to ANSI Class 2500 |
Temperature Rating | -20°F to 1000°F |
Connection Type | Flanged, Threaded, Welded |
Application | Boiler Feedwater, Power Generation, Chemical Processing, Oil and Gas, Water Treatment, HVAC |
Conclusion
A stop check valve is a vital component in fluid handling systems, offering both backflow prevention and manual flow control. Its versatility and reliability make it an essential choice for various industries. By understanding its functions, applications, and benefits, you can make informed decisions when selecting and implementing these valves in your systems. For high quality stop check valve solutions, contact us today.
FAQ
Q: What is the main function of a check valve?
A: The main function of a check valve is to prevent backflow and provide manual shut-off capabilities.
Q: In what industries are stop check valves commonly used?
A: Stop check valves are commonly used in industries such as power generation, chemical processing, oil and gas, and water treatment.
Q: How does a check valve differ from a regular check valve?
A: A check valve allows for manual shut-off, while a regular check valve operates solely on fluid pressure.
Q: What materials are stop check valves typically made of?
A: Common materials include carbon steel, stainless steel, alloy steel, and cast iron.