Introduction
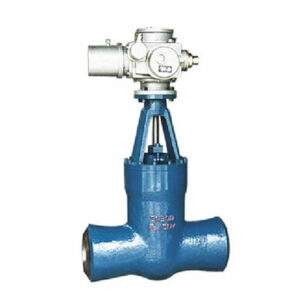
Power stations, the backbone of our modern electrical infrastructure, rely on a complex network of systems to generate electricity. Within this intricate machinery, valves play a pivotal role in controlling the flow of fluids and gases. Among these, power station gate valves stand out as simple yet highly effective devices. This comprehensive guide delves into the nuances of power station gate valves, exploring their design, applications, and maintenance.
What is a Power Station Gate Valve?
A power station gate valve is a type of linear motion valve designed to completely open or close a flow passage. It comprises a gate or wedge-shaped element that moves perpendicular to the flow direction. When fully open, the gate offers minimal resistance to fluid flow, ensuring efficient and unimpeded operation. This fundamental design principle makes gate valves suitable for a wide range of applications within power plants.
Applications of Power Station Gate Valves
Power station gate valves find widespread application in various critical systems within power plants:
- Steam Systems: Controlling the flow of high-pressure steam in boilers, turbines, and condensers.
- Water Systems: Regulating the flow of water for cooling, feedwater, and condensate systems.
- Fuel Systems: Controlling the flow of fuel, such as coal, oil, or natural gas, to the combustion chamber.
- Auxiliary Systems: Used in various auxiliary systems, including lubricating oil systems, compressed air systems, and hydraulic systems.
Design and Construction
The design of a power station gate valve is relatively straightforward, yet crucial for its performance and durability. Key components include:
- Body: The main housing of the valve, providing structural support and containing the flow passage. It is typically made of cast iron, carbon steel, or stainless steel, depending on the application.
- Gate: The movable element that controls the flow, often made of corrosion-resistant materials like stainless steel or alloy steel.
- Stem: Connects the gate to the operating mechanism, allowing for precise control of the valve’s position.
- Seat: The stationary surface against which the gate seals to prevent leakage. It is usually made of a hard, wear-resistant material.
- Operating Mechanism: Can be manual, hydraulic, or electric, depending on the valve size, operating conditions, and control requirements.
Materials of Construction
The selection of materials for power station gate valves is influenced by factors such as temperature, pressure, and the nature of the fluid being handled. Common materials include:
- Carbon Steel: A versatile material suitable for general-purpose applications.
- Stainless Steel: Offers excellent corrosion resistance and is ideal for high-temperature and corrosive environments.
- Cast Iron: A cost-effective option for less demanding applications.
- Alloy Steels: Provide enhanced strength, toughness, and resistance to specific chemicals, making them suitable for critical applications.
Advantages of Power Station Gate Valves
Power station gate valves offer several advantages that make them a preferred choice for various applications:
- Simple Design: Their straightforward design contributes to easy operation and maintenance.
- Full Flow: When fully open, they offer minimal resistance to fluid flow, ensuring efficient operation.
- Tight Shutoff: They can provide a leak-tight seal when fully closed, preventing fluid loss and ensuring safety.
- Bidirectional Flow: They can handle flow in either direction, increasing their versatility.
- Durability: They are designed to withstand harsh operating conditions and provide long-term reliable service.
Selection Criteria for Power Station Gate Valves
When selecting a power station gate valve, several factors must be carefully considered:
- Pipe Size: The diameter of the pipe to which the valve will be connected.
- Pressure Rating: The maximum pressure the valve can withstand without compromising its integrity.
- Temperature Rating: The maximum temperature the valve can handle without degrading its performance.
- Material Compatibility: The compatibility of the valve material with the fluid being handled to prevent corrosion and other issues.
- Operating Conditions: The frequency of operation, cycle life, and environmental conditions to which the valve will be exposed.
Maintenance and Inspection
Regular maintenance and inspection of power station gate valves are essential to ensure their continued reliable operation. Key maintenance activities include:
- Lubrication: Applying appropriate lubricant to moving parts to reduce friction and wear.
- Packing Inspection: Checking the packing for leaks, wear, and damage, and replacing it as needed.
- Seat Inspection: Inspecting the seat for erosion, pitting, or other signs of damage.
- Operating Mechanism Inspection: Checking the operating mechanism for proper function, lubrication, and alignment.
- Body Inspection: Inspecting the valve body for cracks, corrosion, or other defects.
Comparison of Gate Valve Types
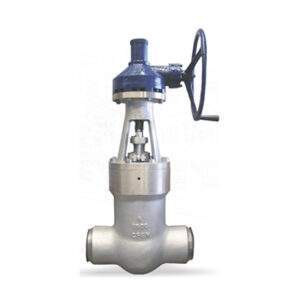
Type | Description | Advantages | Disadvantages |
---|---|---|---|
Parallel Disc | Two parallel discs that come together to form a seal. | Good for high-pressure applications, provides excellent shutoff. | Can be more prone to sticking and requires precise alignment. |
Wedge | A wedge-shaped gate that moves perpendicular to the flow. | Simple design, easy to operate, and provides full flow when open. | May require more force to open and close, especially in large sizes. |
Knife Gate | A flat gate that moves perpendicular to the flow. | Suitable for slurries and abrasive materials, provides excellent shutoff. | Can be prone to erosion and requires careful maintenance. |
Conclusion
Power station gate valves are indispensable components of power plants, providing reliable control of fluid flow in various critical systems. By understanding their design, applications, and maintenance requirements, engineers and operators can ensure the optimal performance of these valves and contribute to the overall efficiency and reliability of power generation facilities.
FAQ
What is the difference between a gate valve and a globe valve?
Gate valves are primarily used for on-off service, while globe valves are better suited for throttling and regulating flow.
How often should power station gate valves be inspected?
The frequency of inspection depends on factors such as operating conditions, fluid properties, and maintenance history. However, regular inspections, at least annually, are recommended.
What are the common causes of gate valve leakage?
Common causes of gate valve leakage include worn packing, damaged seats, misaligned discs, and improper installation.
Can gate valves be used for throttling?
While gate valves can be used for throttling, it is not their primary function. Continuous throttling can lead to increased wear and reduced valve life.
What are the safety considerations when working with power station gate valves?
When working with power station gate valves, it is essential to follow safety procedures, including lockout-tagout procedures, to prevent accidents and injuries.