Introduction
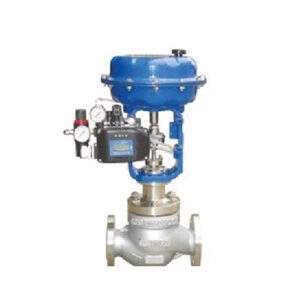
Pneumatic systems are ubiquitous in modern industry, powering everything from automated assembly lines to complex robotic systems. At the heart of these systems lies the pneumatic flow control valve, a seemingly simple device with a crucial role: regulating the flow of compressed air. This precise control is essential for optimizing system performance, ensuring smooth operation, and maximizing efficiency. This blog post delves into the world of pneumatic flow control valves, exploring their various types, functionalities, and diverse applications across numerous industries. We will explore how these valves contribute to overall system efficiency and reliability. Understanding the nuances of pneumatic flow control valve applications is crucial for engineers, technicians, and anyone working with pneumatic systems.
What is a Pneumatic Flow Control Valve?
A pneumatic flow control valve is a mechanical device designed to regulate the rate at which compressed air flows through a pneumatic system. By adjusting the valve’s orifice, or opening, the flow rate can be increased or decreased, thereby controlling the speed and force of pneumatic actuators, such as cylinders and motors. These valves are essential for achieving precise control over pneumatic operations, ensuring smooth and consistent performance. They are available in various designs and configurations to suit different application requirements.
Types of Pneumatic Flow Control Valves
Pneumatic flow control valves come in various designs, each with its unique characteristics and applications. Understanding these different types is crucial for selecting the right valve for a specific pneumatic system.
Needle Valves
Needle valves are one of the simplest and most common types of pneumatic flow control valves. They use a tapered needle that moves in and out of an orifice to control the flow rate. These valves offer fine control over flow but are generally not suitable for applications requiring rapid adjustments.
Check Valves
Check valves allow airflow in only one direction, preventing backflow. They are often used in conjunction with other flow control valves to ensure unidirectional flow in specific parts of a pneumatic circuit.
One-Way Flow Control Valves (Meter-In/Meter-Out)
One-way flow control valves, also known as meter-in or meter-out valves, combine a needle valve with a check valve. These valves allow free flow in one direction and controlled flow in the opposite direction. Meter-in control restricts airflow entering the actuator, while meter-out control restricts airflow exiting the actuator.
Quick Exhaust Valves
Quick exhaust valves are designed to rapidly exhaust air from pneumatic cylinders, increasing their speed. They are particularly useful in applications requiring fast cycling times.
Key Features and Considerations of Pneumatic Flow Control Valves
Selecting the appropriate pneumatic flow control valve for a specific application requires careful consideration of several key features and factors.
Flow Rate and Cv Value
The flow rate, typically measured in standard cubic feet per minute (SCFM) or liters per minute (L/min), indicates the volume of air that can pass through the valve per unit of time. The Cv value, or flow coefficient, is a measure of the valve’s capacity to allow fluid flow. A higher Cv value indicates a greater flow capacity.
Pressure Rating
The pressure rating specifies the maximum pressure the valve can withstand without damage or malfunction. It is crucial to select a valve with a pressure rating that meets or exceeds the maximum operating pressure of the pneumatic system.
Temperature Range
The operating temperature range defines the acceptable temperature limits for the valve’s operation. Operating the valve outside this range can lead to performance degradation or failure.
Material Compatibility
The valve’s materials must be compatible with the working fluid (compressed air) and the surrounding environment. Corrosion-resistant materials, such as stainless steel, are often used in harsh environments.
Pneumatic Flow Control Valve Applications Across Industries
Pneumatic flow control valves find widespread use in various industries due to their versatility, reliability, and cost-effectiveness.
Manufacturing and Automation
In manufacturing and automation, pneumatic flow control valves are essential for controlling the speed and movement of robotic arms, pneumatic cylinders, and other automated machinery. They ensure precise and consistent operation, improving production efficiency and quality.
Packaging and Food Processing
In the packaging and food processing industries, pneumatic systems are used for tasks such as filling, sealing, and labeling. Flow control valves play a crucial role in ensuring accurate and efficient packaging processes.
Automotive Industry
The automotive industry utilizes pneumatic systems for various applications, including assembly line operations, robotic welding, and painting. Pneumatic flow control valves are vital for controlling the speed and precision of these processes.
Medical Devices
Pneumatic systems are also employed in medical devices, such as ventilators and surgical instruments. Flow control valves ensure precise control of air and gas flow, which is critical for patient safety and treatment effectiveness.
Aerospace
In the aerospace industry, pneumatic systems are used for various aircraft functions, including landing gear control and flight control surfaces. Reliable and precise flow control is essential for safe and efficient aircraft operation.
Benefits of Using Pneumatic Flow Control Valves
Utilizing pneumatic flow control valves offers numerous advantages in pneumatic systems.
Precise Flow Control
These valves offer precise control over airflow, enabling accurate and consistent operation of pneumatic actuators.
Improved System Efficiency
By optimizing airflow, flow control valves can improve system efficiency and reduce energy consumption.
Enhanced System Reliability
Properly selected and installed flow control valves contribute to the overall reliability and longevity of pneumatic systems.
Cost-Effectiveness
Pneumatic flow control valves are generally cost-effective compared to other flow control methods.
Understanding Pneumatic Flow Control Valve Specifications
Understanding the specifications of a pneumatic flow control valve is essential for selecting the correct valve for a given application. The following table illustrates some key specifications and their significance.
Specification | Description | Significance |
---|---|---|
Port Size | The size of the inlet and outlet ports. | Determines the connection size and flow capacity. |
Flow Rate (Cv) | The flow coefficient, indicating the valve’s flow capacity. | A higher Cv value indicates greater flow capacity. |
Pressure Rating | The maximum pressure the valve can withstand. | Must exceed the system’s maximum operating pressure. |
Operating Temperature | The acceptable temperature range for valve operation. | Ensures reliable performance within the operating environment. |
Material | The material of construction (e.g., brass, stainless steel). | Determines compatibility with the working fluid and environment. |
Adjustment Type | The method of adjusting the flow rate (e.g., needle, screw). | Affects the precision and ease of adjustment. |
Mounting Type | The method of mounting the valve (e.g., inline, panel). | Determines the installation method. |
Troubleshooting Common Issues with Pneumatic Flow Control Valves
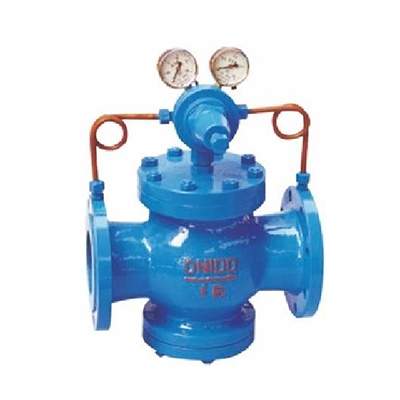
Like any mechanical device, pneumatic flow control valves can experience problems that affect their performance. Here are some common issues and troubleshooting tips:
Leakage
Leakage can occur due to worn seals, loose connections, or damaged valve bodies. Inspect the valve for visible damage and replace any worn or damaged parts. Ensure all connections are tight and properly sealed.
Restricted Flow
Restricted flow can be caused by debris buildup, a clogged orifice, or an improperly adjusted valve. Clean the valve and orifice to remove any debris. Ensure the valve is adjusted correctly.
Erratic Operation
Erratic operation can result from fluctuating pressure, a malfunctioning check valve, or a damaged valve mechanism. Check the system pressure for stability. Inspect the check valve for proper operation. Examine the valve mechanism for any damage.
Conclusion
Pneumatic flow control valves are indispensable components in modern pneumatic systems. Their ability to precisely regulate airflow is crucial for achieving optimal system performance, efficiency, and reliability. By understanding the different types of valves, their key features, and their diverse applications, engineers and technicians can effectively select and utilize these devices to maximize the benefits of pneumatic technology across a wide range of industries. Choosing the right pneumatic flow control valve is essential for ensuring smooth, efficient, and reliable operation of pneumatic systems. From manufacturing to medical devices, these valves play a vital role in countless applications, contributing to advancements across various industries.
FAQ
What is the purpose of a pneumatic flow control valve?
A pneumatic flow control valve regulates the rate at which compressed air flows through a pneumatic system, controlling the speed and force of pneumatic actuators.
How do I choose the right pneumatic flow control valve?
Selecting the right valve involves considering factors such as flow rate, pressure rating, temperature range, material compatibility, and application requirements.
What are the different types of pneumatic flow control valves?
Common types include needle valves, check valves, one-way flow control valves (meter-in/meter-out), and quick exhaust valves.
What is the Cv value of a pneumatic flow control valve?
The Cv value, or flow coefficient, is a measure of the valve’s capacity to allow fluid flow. A higher Cv value indicates a greater flow capacity.