Welcome to My Blog!
Before we dive into the content, I’d love for you to join me on my social media platforms where I share more insights, engage with the community, and post updates. Here’s how you can connect with me:
Facebook:https://www.facebook.com/profile.php?id=61563865935136
Now, let’s get started on our journey together. I hope you find the content here insightful, engaging, and valuable.
Introduction
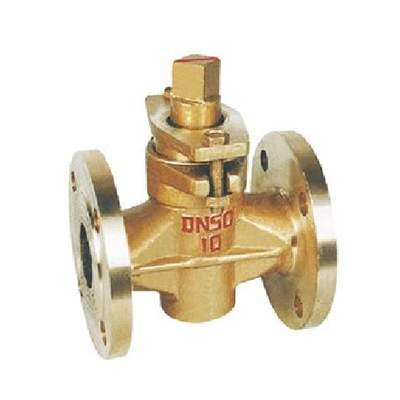
Plug valves are essential components in various industrial applications, known for their simple design and reliable performance. Understanding plug valve dimensions is crucial for proper installation, operation, and maintenance. This knowledge ensures compatibility with existing systems and facilitates efficient replacement when necessary. This comprehensive guide delves into the intricacies of plug valve dimensions, covering various aspects from basic terminology to advanced considerations, empowering engineers and technicians to make informed decisions.
Understanding the Basics of Plug Valve Dimensions
Before diving into specifics, it’s important to grasp the fundamental concepts related to plug valve dimensions. These include:
- Nominal Size (DN): This refers to the approximate inside diameter of the valve’s connection, expressed in millimeters. It’s a nominal value, not an exact measurement, and is often used for general identification.
- Valve Size: This indicates the size of the valve, often expressed in inches or millimeters. It’s related to the nominal size but may not be identical and can be influenced by other design factors.
- End Connection: This describes how the valve connects to the piping system, such as flanged, threaded, or welded. The type of end connection significantly impacts installation procedures.
- Face-to-Face Dimension: This is the distance between the end connections of the valve. This dimension is critical for ensuring proper fit within the piping system.
- Overall Height: This is the total height of the valve, including the actuator or handle. This measurement is important for clearance considerations during installation and operation.
- Operating Pressure and Temperature: These parameters define the limits within which the valve can operate safely and effectively. Exceeding these limits can lead to valve failure and potential hazards.
Importance of Accurate Plug Valve Dimensions
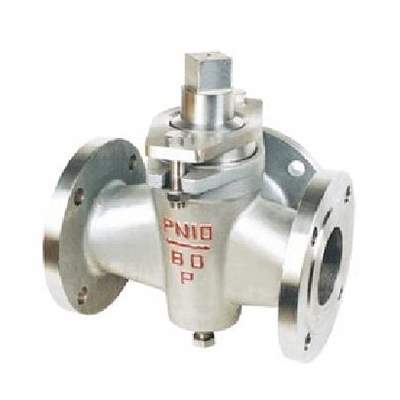
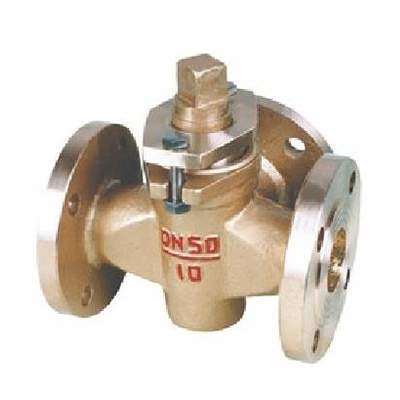
Accurate plug valve dimensions are paramount for several reasons:
- Interchangeability: Standardized dimensions ensure that valves from different manufacturers can be interchanged without significant modifications. This simplifies maintenance and reduces downtime.
- Installation: Precise dimensions are necessary for proper installation, preventing leaks and ensuring efficient operation. Incorrect dimensions can lead to costly rework and delays.
- Maintenance: Knowing the exact dimensions facilitates maintenance and repair, as replacement parts can be easily identified and procured. This reduces the time required for repairs and minimizes production interruptions.
- System Design: Accurate dimensions are crucial for designing piping systems that accommodate the valves seamlessly. Properly accounting for valve dimensions prevents clashes with other components and ensures efficient flow.
Types of Plug Valves and Their Dimensions
Plug valves come in various types, each with its unique plug valve dimensions:
- Cylindrical Plug Valves: These valves have a cylindrical plug with a port that aligns with the pipeline when open. They are simple in design and offer good flow characteristics.
- Conical Plug Valves: These valves have a conical plug, offering a tighter seal and better flow control. The tapered design provides a more secure closure and reduces the risk of leakage.
- Eccentric Plug Valves: These valves have an offset plug, reducing friction and wear. This design extends the valve’s lifespan and reduces operating torque.
The plug valve dimensions for each type vary depending on the size, pressure rating, and specific design. These variations must be considered when selecting a valve for a particular application.
Factors Affecting Plug Valve Dimensions
Several factors influence plug valve dimensions:
- Pressure Rating: Higher pressure ratings often require larger and more robust valves, affecting their dimensions. Higher pressure necessitates thicker walls and stronger materials, increasing overall size.
- Temperature: Extreme temperatures can necessitate special materials and designs, which may alter the dimensions. High temperatures can cause expansion, while low temperatures can cause contraction, both of which need to be accounted for.
- Application: The specific application of the valve, such as throttling or on/off control, can influence its dimensions. Throttling applications may require different plug and port configurations than on/off applications.
- Fluid Type: The type of fluid being handled can also affect the choice of materials and dimensions. Corrosive fluids may require specialized materials that impact the valve’s overall size.
Plug Valve Dimensions Chart
The following table provides a general overview of plug valve dimensions for different nominal sizes. Please note that these are approximate values and may vary depending on the manufacturer and specific valve design. Always consult the manufacturer’s documentation for precise dimensions.
Nominal Size (DN) | Valve Size (inches) | Face-to-Face Dimension (mm) | Overall Height (mm) |
---|---|---|---|
15 | 1/2 | 110 | 150 |
20 | 3/4 | 130 | 170 |
25 | 1 | 150 | 190 |
32 | 1 1/4 | 160 | 210 |
40 | 1 1/2 | 180 | 230 |
50 | 2 | 210 | 260 |
65 | 2 1/2 | 230 | 290 |
80 | 3 | 260 | 320 |
100 | 4 | 300 | 370 |
Measuring Plug Valve Dimensions
Accurately measuring plug valve dimensions is essential for various purposes. Here are some tips for measuring different dimensions:
- Face-to-Face Dimension: Measure the distance between the end connections using a caliper or ruler. Ensure the measuring tool is properly calibrated for accurate results.
- Overall Height: Measure the vertical distance from the bottom of the valve to the top of the actuator or handle. Be sure to include any mounting brackets or other extensions in the measurement.
- End Connection: Identify the type of end connection and measure its dimensions accordingly. This may involve measuring flange diameter, thread size, or weld preparation.
Importance of Standards in Plug Valve Dimensions
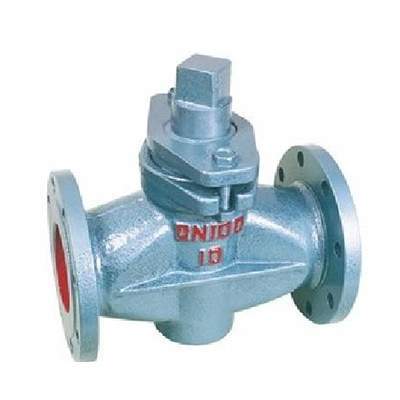
Standards play a crucial role in ensuring consistency and compatibility in plug valve dimensions. Adhering to relevant standards, such as ASME B16.10 or ISO 5752, guarantees that valves meet specific requirements and can be easily integrated into piping systems. These standards promote interoperability and reduce the risk of installation errors.
Conclusion
Understanding plug valve dimensions is fundamental for engineers, technicians, and anyone involved in the selection, installation, and maintenance of these essential components. This comprehensive guide has provided insights into various aspects of plug valve dimensions, from basic terminology to advanced considerations. By adhering to standards and paying close attention to accurate measurements, you can ensure the optimal performance and longevity of your plug valves. Properly specified and installed plug valves contribute to efficient and safe operation of industrial processes.
FAQ
Q: How do I determine the correct plug valve size for my application?
A: Consider the flow rate, pressure, temperature, and fluid type to select the appropriate valve size. Consult valve selection charts and manufacturer recommendations for guidance.
Q: What are the common end connection types for plug valves?
A: Common end connections include flanged, threaded, and welded. The choice of end connection depends on the piping system and application requirements.
Q: How do I measure the face-to-face dimension of a plug valve?
A: Measure the distance between the end connections using a caliper or ruler. Ensure the valve is in a closed position for accurate measurement.
Q: Why are standards important for plug valve dimensions?
A: Standards ensure consistency and compatibility, allowing for interchangeability and proper integration. They also provide guidelines for design and testing, ensuring quality and safety.