Welcome to My Blog!
Before we dive into the content, I’d love for you to join me on my social media platforms where I share more insights, engage with the community, and post updates. Here’s how you can connect with me:
Facebook:https://www.facebook.com/profile.php?id=61563865935136
Now, let’s get started on our journey together. I hope you find the content here insightful, engaging, and valuable.
Introduction
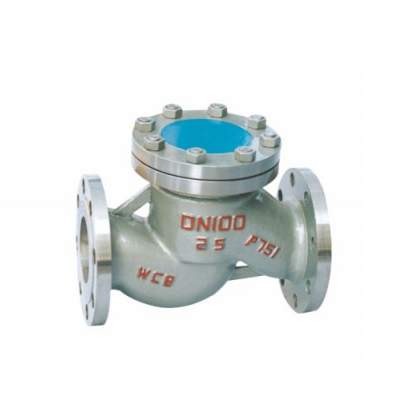
In various industrial applications, maintaining system integrity and preventing backflow are paramount. This is where the non return check valve plays a crucial role. A non return check valve, also known as a one-way valve, allows fluid to flow in one direction while preventing it from flowing back. This simple yet vital component safeguards systems from potential damage and ensures operational efficiency. The strategic implementation of a non return check valve can significantly extend the lifespan of piping systems and connected equipment. In this comprehensive guide, we will delve into the various uses, types, and benefits of the non return check valve. We will also touch upon the frequently asked questions regarding the non return check valve, providing clarity for both novice and experienced users.
Understanding the Non Return Check Valve Functionality
The core function of a non return check valve is to maintain unidirectional flow. This is achieved through a mechanism that opens when fluid pressure exceeds a certain threshold, allowing flow. When the pressure drops or reverses, the mechanism closes, preventing backflow. This simple principle is critical in applications where backflow can lead to contamination, damage, or system failure. The non return valve is designed to be simple, reliable, and efficient. Its design minimizes pressure drop while maximizing the assurance of one-way flow, contributing to overall system performance.
Key Applications of the Non Return Check Valve
The non return check valve is utilized across numerous industries, each with unique requirements. Here are some key applications:
- Water and Wastewater Treatment: Preventing backflow in water treatment plants is essential to maintain purity and prevent contamination. Non return check valve plays a critical role in these applications. They are especially critical in preventing treated water from re-entering the source water supply.
- Chemical Processing: In chemical plants, backflow can lead to dangerous reactions or contamination of sensitive materials. The non return valve is essential for safety. They prevent the mixing of incompatible chemicals, which could result in hazardous situations.
- Oil and Gas Industry: Pipelines and refineries rely on non return valve to prevent backflow and maintain pressure integrity. The non return valve also ensure the safety of the working environment. They are crucial for maintaining consistent pressure in pipelines and preventing damage to pumping equipment.
- HVAC Systems: Heating, ventilation, and air conditioning systems use non return valve to ensure proper flow and prevent backflow, which can lead to inefficiencies. They help in maintaining consistent temperature and pressure within the system, optimizing energy consumption.
- Medical Equipment: In medical applications, non return check valve ensures the accurate and safe delivery of fluids and gases. They are critical in devices such as infusion pumps and ventilators, where precise flow control is vital.
- Irrigation Systems: They are used to prevent backflow from irrigation systems into potable water supplies. This prevents contamination of drinking water sources from fertilizers or pesticides used in irrigation.
Types of Non Return Check Valve
Several types of non return valve are available, each designed for specific applications and pressure requirements. Here are some common types:
- Swing Check Valve: This type uses a hinged disc that swings open to allow forward flow and closes to prevent backflow. They are suitable for low-pressure applications and are known for their simplicity and reliability.
- Lift Check Valve: A lift check valve uses a disc that lifts vertically to allow flow and drops to prevent backflow. These valves are commonly used in high-pressure applications and are designed to minimize pressure drop.
- Ball Check Valve: This valve uses a ball that moves to allow flow and seats to prevent backflow. Ball check valves are effective in handling viscous fluids and are often used in pumping applications.
- Spring Check Valve: This valve uses a spring to keep the disc or ball closed, opening only when sufficient pressure is applied. They provide rapid closure, preventing water hammer and are often used in applications requiring quick response.
- Duckbill Check Valve: This is a flexible valve that allows flow in one direction by opening a slit and closes to prevent backflow. Duckbill valves are ideal for handling slurries and wastewater due to their ability to handle solids.
Benefits of Using a Non Return Check Valve
Implementing a non return check valve offers several significant benefits:
- Prevention of Backflow: The primary benefit is preventing backflow, which protects systems from contamination and damage. This is essential for maintaining the integrity of fluid systems and preventing costly repairs.
- System Integrity: Ensuring unidirectional flow maintains system integrity and operational efficiency. Consistent flow prevents pressure fluctuations and ensures that systems operate as designed.
- Safety: In industries dealing with hazardous materials, non return valve enhances safety by preventing dangerous backflow. They minimize the risk of accidents and ensure a safe working environment.
- Reduced Maintenance: By preventing backflow, non return valve reduces the need for frequent maintenance and repairs. This results in lower operational costs and increased system uptime.
- Enhanced Efficiency: Maintaining proper flow ensures systems operate at peak efficiency. This leads to energy savings and improved overall system performance.
Material Selection for Non Return Check Valve
Choosing the right material for a non return check valve is crucial for ensuring its longevity and performance. The material must be compatible with the fluid being handled and the operating conditions. Common materials include:
- Stainless Steel: Known for its corrosion resistance and durability. It is ideal for applications involving corrosive fluids or high temperatures.
- Brass: Suitable for water and low-pressure applications. Brass offers good corrosion resistance in water applications and is cost-effective.
- PVC: Ideal for chemical applications due to its resistance to many chemicals. PVC valves are lightweight and easy to install, making them a popular choice in chemical processing.
- Cast Iron: Robust and suitable for high-pressure applications. Cast iron provides excellent durability and strength, making it suitable for demanding industrial environments.
Installation and Maintenance of Non Return Check Valve
Proper installation and regular maintenance are essential for ensuring the non return valve functions correctly. Here are some key considerations:
- Installation: Follow the manufacturer’s instructions for proper installation. Ensure the valve is installed in the correct orientation to prevent backflow.
- Inspection: Regularly inspect the valve for signs of wear or damage. Look for leaks, corrosion, or any signs of mechanical failure.
- Cleaning: Clean the valve to remove any debris or buildup that could affect its operation. Regular cleaning prevents blockages and ensures smooth operation.
- Replacement: Replace the valve if it shows signs of significant wear or damage. Timely replacement prevents system failures and ensures ongoing safety.
Non Return Check Valve Selection Criteria
Choosing the correct non return check valve involves considering several factors:
- Fluid Type: The type of fluid being handled will determine the material and type of valve needed. Corrosive or abrasive fluids require specialized materials and valve designs.
- Pressure and Temperature: The operating pressure and temperature will influence the valve’s design and material selection. High-pressure and high-temperature applications require robust valve designs and materials.
- Flow Rate: The required flow rate will determine the size and type of valve needed. Oversized valves can lead to inefficiency, while undersized valves can restrict flow.
- Installation Requirements: The installation environment and requirements will affect the valve’s design. Consider factors such as space limitations and connection types.
Non Return Check Valve Specifications Table
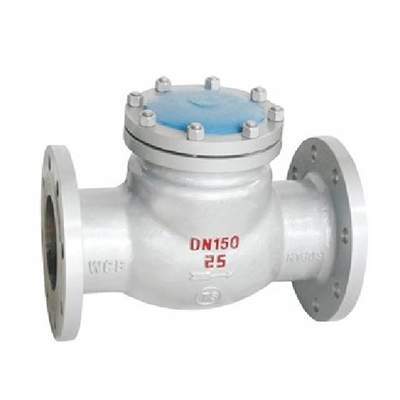
Featu | Specification |
---|---|
Valve Type | Swing, Lift, Ball, Spring, Duckbill |
Material | Stainless Steel, Brass, PVC, Cast Iron |
Pressure Rating | Varies based on application |
Temperature Rating | Varies based on material |
Size Range | Various sizes available |
Connection Type | Threaded, Flanged, Welded |
Application examples | water, gas, chemicals, oil |
Conclusion
The non return check valve is a crucial component in numerous industrial applications, ensuring system safety and efficiency. By understanding its functionality, types, and benefits, you can make informed decisions when selecting and implementing these valves. To ensure your systems are running safely and efficiently, consider the quality non return check valve we offer. Contact us today to learn more and make your purchase, and secure the best possible results for your operation.
FAQ
What is a non return check valve?
A non return check valve is a valve that allows fluid to flow in one direction and prevents it from flowing back. This ensures that fluid systems operate efficiently and safely by maintaining unidirectional flow.
Where are non return check valve used?
Non return check valve are used in various industries, including water treatment, chemical processing, oil and gas, HVAC, and medical equipment. They are essential components in any system where backflow could cause damage or contamination.
How do I choose the right non return check valve?
Consider the fluid type, pressure, temperature, flow rate, and installation requirements. Matching the valve to the specific application ensures optimal performance and longevity.
What are the benefits of using a non return check valve?
They prevent backflow, maintain system integrity, enhance safety, reduce maintenance, and improve efficiency. These benefits contribute to overall system reliability and cost-effectiveness.