Welcome to My Blog!
Before we dive into the content, I’d love for you to join me on my social media platforms where I share more insights, engage with the community, and post updates. Here’s how you can connect with me:
Facebook: https://www.facebook.com/profile.php?id=61563865935136
Now, let’s get started on our journey together. I hope you find the content here insightful, engaging, and valuable.
Introduction
In the realm of fluid power, hydraulic systems play a crucial role in various industries, from manufacturing and construction to aerospace and agriculture. At the heart of these systems lie hydraulic control valves, which are essential components responsible for directing, regulating, and controlling the flow of hydraulic fluid. A control valve hydraulic system’s performance depends heavily on the proper selection and application of these valves. This comprehensive guide delves into the world of hydraulic control valves, exploring their types, functions, applications, and key considerations for optimal performance. Understanding control valve hydraulic principles is crucial for anyone working with or designing hydraulic systems.
Types of Hydraulic Control Valves
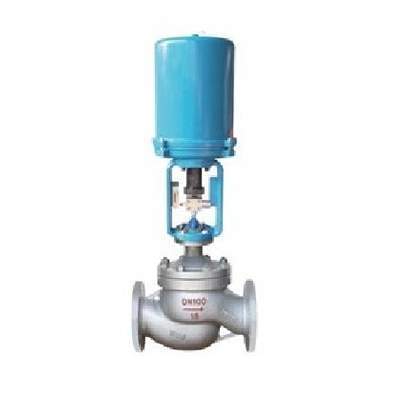
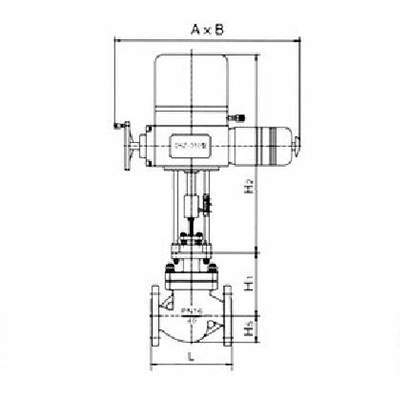
Hydraulic control valves are categorized based on their function, which includes controlling pressure, flow rate, and direction of hydraulic fluid. Each type serves a specific purpose in a control valve hydraulic circuit.
Pressure Control Valves Hydraulic
These valves regulate the pressure within a hydraulic system. They are crucial for preventing overpressure, maintaining system stability, and ensuring safe operation. Common types include:
- Relief Valves: These valves protect the system from overpressure by opening when the pressure exceeds a predetermined setpoint, diverting excess fluid back to the reservoir.
- Pressure Reducing Valves: These valves reduce the pressure in a specific part of the system to a lower level than the main system pressure.
- Sequence Valves: These valves control the sequence of operations in a hydraulic circuit, allowing one operation to occur only after another has been completed.
- Unloading Valves: These valves unload the pump when the system reaches a certain pressure, reducing power consumption.
Flow Control Valves Hydraulic
These valves regulate the flow rate of hydraulic fluid, controlling the speed of actuators such as cylinders and motors. Key types include:
- Throttle Valves: These simple valves restrict the flow of fluid, creating a pressure drop and reducing the flow rate.
- Flow Control Valves with Check Valves: These valves combine a throttle valve with a check valve, allowing free flow in one direction and restricted flow in the other.
- Pressure-Compensated Flow Control Valves: These valves maintain a constant flow rate regardless of pressure variations in the system.
Directional Control Valves Hydraulic
These valves direct the flow of hydraulic fluid to different parts of the system, controlling the direction of movement of actuators. They are available in various configurations, including:
- Check Valves: These valves allow flow in only one direction, preventing backflow.
- Shuttle Valves: These valves select the higher pressure from two sources to supply a single outlet.
- Spool Valves: These valves use a sliding spool to control the flow path. They are available in various configurations, such as 2-way, 3-way, and 4-way valves.
- Rotary Valves: These valves use a rotating element to control the flow path.
Servo Valves and Proportional Valves Hydraulic
These are more advanced types of hydraulic control valves that offer precise control over flow and pressure.
- Servo Valves: These valves provide highly accurate and responsive control, typically used in closed-loop control systems.
- Proportional Valves: These valves offer proportional control of flow or pressure based on an electrical input signal.
Hydraulic Control Valve Operation and Applications
The operation of a control valve hydraulic system depends on the type of valve and its specific design. In general, these valves use mechanical, hydraulic, electrical, or pneumatic signals to control the position of internal components, such as spools, poppets, or balls, which in turn regulate the flow of hydraulic fluid.
Hydraulic Control Valve Applications
Hydraulic control valves are found in a wide range of applications across various industries:
- Manufacturing: Machine tools, presses, injection molding machines.
- Construction: Excavators, cranes, loaders.
- Aerospace: Aircraft flight control systems, landing gear.
- Agriculture: Tractors, harvesters, sprayers.
- Material Handling: Forklifts, conveyors.
- Automotive: Power steering, braking systems.
Factors Affecting Control Valve Hydraulic Performance
Several factors can affect the performance of hydraulic control valves:
- Fluid Properties: Viscosity, temperature, and contamination of the hydraulic fluid.
- Valve Design: Orifice size, spool design, and internal leakage.
- System Pressure and Flow Rate: Operating pressure and flow rate can influence valve performance.
- Environmental Conditions: Temperature, humidity, and vibration can affect valve reliability.
Selection and Maintenance of Hydraulic Control Valves
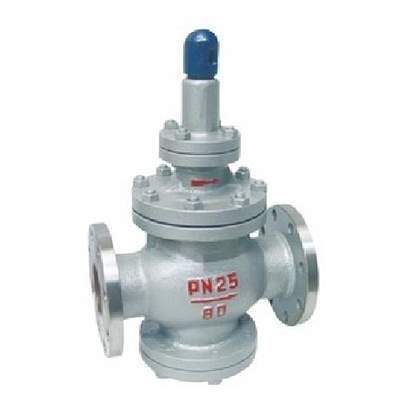
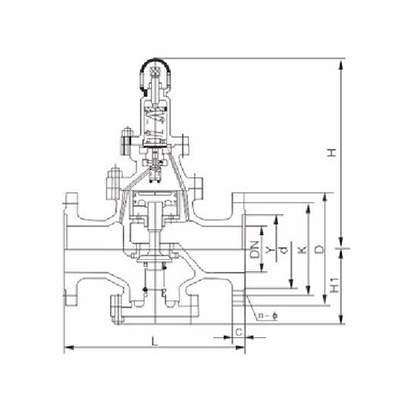
Selecting the appropriate hydraulic control valve is crucial for optimal system performance. Key considerations include:
- System Requirements: Pressure, flow rate, and direction of flow.
- Valve Type and Size: Choosing the correct type and size of valve for the application.
- Operating Conditions: Temperature, pressure, and environmental conditions.
- Installation and Maintenance: Proper installation and regular maintenance are essential for reliable operation.
Hydraulic Control Valve Maintenance
Regular maintenance is crucial for ensuring the long-term reliability and performance of hydraulic control valves. Key maintenance tasks include:
- Fluid Filtration: Maintaining clean hydraulic fluid is essential for preventing valve wear and malfunction.
- Leak Checks: Regularly checking for leaks and repairing them promptly.
- Visual Inspections: Inspecting valves for wear, damage, or contamination.
- Testing and Adjustment: Periodically testing and adjusting valves to ensure proper operation.
Comparison of Hydraulic Control Valve Types
The following table provides a comparison of different types of hydraulic control valves based on their function and characteristics:
Valve Type | Function | Characteristics | Applications |
---|---|---|---|
Relief Valve | Protects system from overpressure | Opens when pressure exceeds setpoint, simple design | Overpressure protection in all hydraulic systems |
Pressure Reducing Valve | Reduces pressure in a specific part of system | Maintains lower pressure in a branch circuit, various types available | Applications requiring different pressures in different parts of the system |
Flow Control Valve | Regulates flow rate | Controls speed of actuators, various types available (throttle, compensated) | Controlling actuator speed in various applications |
Directional Control Valve | Directs flow of hydraulic fluid | Controls direction of actuator movement, various configurations (2-way, 3-way, 4-way) | Controlling actuator direction in all hydraulic systems |
Check Valve | Allows flow in one direction only | Prevents backflow, simple and reliable | Preventing backflow in various hydraulic circuits |
Servo Valve | Precise control of flow and pressure | Highly accurate and responsive, used in closed-loop control systems | High-precision applications requiring accurate control |
Proportional Valve | Proportional control of flow or pressure | Controls flow or pressure based on electrical input, less precise than servo valves | Applications requiring variable control of flow or pressure |
This table provides a useful overview for comparing different control valve hydraulic options.
FAQ
What is the primary function of a hydraulic control valve?
The primary function is to control the flow of hydraulic fluid, which in turn controls the operation of hydraulic actuators.
How do I choose the right size hydraulic control valve?
The valve size should be selected based on the system’s flow rate requirements. Using a valve that is too small will restrict flow, while a valve that is too large can lead to instability.
What are the common causes of hydraulic control valve failure?
Common causes include contamination of the hydraulic fluid, wear of internal components, and improper installation or maintenance.
How can I troubleshoot a malfunctioning hydraulic control valve?
Troubleshooting involves checking for leaks, inspecting the valve for damage, and testing its operation. It’s often helpful to consult a hydraulic schematic.
What is the difference between a 2-way and a 3-way directional control valve?
A 2-way valve has two ports and controls flow in one direction. A 3-way valve has three ports and can direct flow to two different outlets.