Introduction
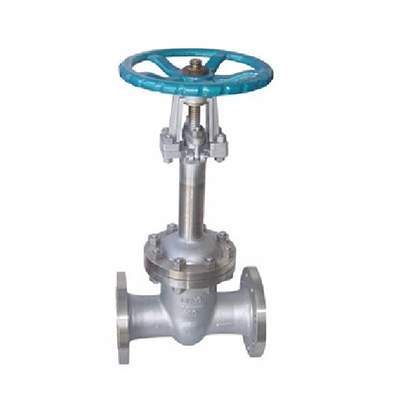
High pressure gate valves are indispensable components in various industries, including oil and gas, chemical processing, and power generation. These valves are engineered to withstand extreme pressures and temperatures, ensuring the safe and efficient operation of piping systems. This comprehensive guide delves into the critical factors that contribute to the quality and durability of high pressure gate valves. We will explore the intricate details of material selection, design considerations, manufacturing processes, and performance characteristics. By understanding these key aspects, engineers and procurement professionals can make informed decisions when selecting valves for specific applications.
Understanding High Pressure Gate Valves
High pressure gate valves are designed to control the flow of fluids by lifting a gate or wedge out of the fluid stream. They are primarily used for on-off applications, but some designs can also provide limited throttling capabilities. The ability of a gate valve to withstand high pressures is largely dependent on its construction, materials, and sealing mechanisms. A well-designed and manufactured high pressure gate valves ensures reliable performance, minimizes maintenance requirements, and contributes to the overall efficiency and safety of industrial processes.
Key Factors Affecting Quality and Durability
Material Selection
The choice of material is a critical factor in determining the performance and longevity of a high pressure gate valves. Common materials include:
- Carbon steel: Cost-effective for general-purpose applications, carbon steel offers a good balance of strength and durability. However, it is susceptible to corrosion, particularly in harsh environments.
- Stainless steel: Renowned for its excellent corrosion resistance and high-temperature capabilities, stainless steel is ideal for applications involving corrosive fluids and elevated temperatures.
- Alloy steel: Offering superior strength and resistance to specific corrosive environments, alloy steel is often used in high-pressure, high-temperature applications.
- Cast iron: While cost-effective, cast iron has lower tensile strength compared to other materials. It is typically used for lower pressure applications.
Design Considerations
- Body design: The body of the valve must be robust enough to withstand internal pressure and external forces. A well-designed body ensures structural integrity and prevents deformation or failure under extreme conditions.
- Sealing mechanism: The sealing mechanism, typically a soft seat or metal-to-metal seat, must provide a leak-tight seal. A reliable sealing mechanism is essential for preventing fluid leakage and maintaining system integrity.
- Stem design: The stem must be strong, corrosion-resistant, and capable of withstanding the forces exerted during valve operation. A well-designed stem ensures smooth and reliable valve operation.
Manufacturing Process
- Casting: Most gate valves are cast from the chosen material. Precision casting techniques ensure accurate dimensions and minimize defects.
- Machining: Precision machining is employed to achieve precise tolerances and smooth surface finishes. Machining processes, such as milling and turning, are used to shape the valve components.
- Heat treatment: Heat treatment processes, such as annealing and tempering, are applied to improve the mechanical properties of the valve, enhancing its strength, toughness, and durability.
Testing and Certification
- Pressure testing: Valves are subjected to hydrostatic pressure tests to verify their strength and integrity. Pressure testing ensures that the valve can withstand the maximum operating pressure without failure.
- Leak testing: Leak tests are conducted to ensure that the valve seals properly. Leak testing identifies any potential leaks or defects in the sealing mechanism.
- Certification: Compliance with industry standards and certifications, such as API, ASME, and ISO, is essential for quality assurance. Certification ensures that the valve meets stringent quality standards and is suitable for specific applications.
Performance Characteristics
- Pressure rating: The maximum pressure a valve can safely withstand.
- Temperature rating: The temperature range at which the valve can operate reliably.
- Cycle life: The number of cycles a valve can undergo before requiring maintenance or replacement.
- Leak rate: The rate at which fluid can leak past the seal.
- Torque: The amount of force required to operate the valve.
Factors to Consider When Selecting a High Pressure Gate Valves
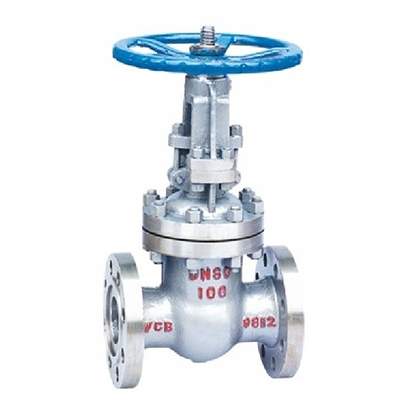
- Operating conditions: Pressure, temperature, fluid compatibility, and cycle frequency are critical factors to consider when selecting a valve.
- Material compatibility: The valve material must be compatible with the fluid being handled to prevent corrosion and other forms of degradation.
- Size and weight: The physical dimensions of the valve must be suitable for the installation and operation.
- Cost: The initial purchase cost and ongoing maintenance costs should be carefully evaluated.
Conclusion
High pressure gate valves are essential components in various industries, ensuring the safe and efficient operation of piping systems. By understanding the factors that influence their quality and durability, engineers and procurement professionals can make informed decisions when selecting valves for specific applications. By carefully considering material selection, design, manufacturing, and testing, it is possible to choose high pressure gate valves that will provide long-term service, minimize downtime, and contribute to the overall reliability and safety of industrial processes.
FAQ
Q: What is a high pressure gate valves?
A: A high pressure gate valves is a type of valve designed to control the flow of high-pressure fluids. It works by lifting a gate or wedge out of the fluid stream to allow flow or lowering it to block the flow.
Q: What are the key factors affecting the quality and durability of a high-pressure gate valve?
A: Key factors include material selection (e.g., carbon steel, stainless steel, alloy steel), design considerations (body design, sealing mechanism, stem design), manufacturing processes (casting, machining, heat treatment), and testing and certification.
Q: How often should high-pressure gate valves be inspected and maintained?
A: The frequency of inspection and maintenance depends on various factors, including operating conditions, fluid properties, and regulatory requirements. Regular inspections, lubrication, and potential replacement of worn parts are crucial for optimal performance and longevity.
Q: What are the common causes of failure in high pressure gate valves?
A: Common causes of failure include corrosion, erosion, cavitation, and improper installation or operation. Regular inspections, proper maintenance, and adherence to manufacturer’s guidelines can help mitigate these issues.
Q: How can I ensure that a high-pressure gate valve is properly sized for my application?
A: Proper sizing is essential for optimal performance and safety. Consider factors such as flow rate, pressure, temperature, and fluid properties. Consult with valve manufacturers or experienced engineers to determine the appropriate valve size for your specific application.