Introduction
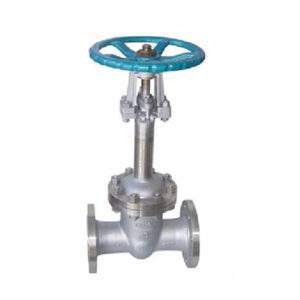
Gate valves are essential components in diverse industrial and commercial applications, serving as crucial control elements within piping systems. They are designed to regulate the flow of fluids and gases by either fully opening or closing the passageway. The selection of the correct gate valve sizes is paramount for ensuring optimal system performance, efficiency, and longevity. An improperly sized gate valve can lead to various issues, including inadequate flow capacity, excessive pressure drop, and even equipment damage.
This comprehensive guide will delve into the intricacies of gate valve sizes, providing you with a thorough understanding of the factors influencing size selection, industry standards, and best practices for choosing the right gate valve for your specific application. We will explore the key considerations, such as flow rate, pressure requirements, material compatibility, and temperature limitations, that must be carefully evaluated to ensure the proper functioning of your piping system.
Understanding Gate Valve Sizes
The size of a gate valve is typically denoted by its nominal pipe size (NPS), which represents the approximate inside diameter of the pipe to which the valve is intended to be connected. NPS is commonly expressed in inches or millimeters. It’s crucial to understand that the NPS is a nominal value and may not precisely correspond to the actual internal diameter of the valve.
Several factors contribute to this discrepancy:
- Wall thickness: The thickness of the valve body and internal components, such as the gate itself, will inevitably reduce the internal diameter compared to the nominal pipe size.
- Manufacturing tolerances: Slight variations in manufacturing processes can result in minor deviations from the intended dimensions.
- Valve design: Different gate valve designs, such as wedge gate valves and parallel disk gate valves, may have slightly different internal diameters even for the same NPS.
Therefore, while NPS provides a general indication of the valve’s size, it’s essential to refer to the valve manufacturer’s specifications for precise dimensions and performance data.
Factors Affecting Gate Valve Sizes Selection
The selection of the appropriate gate valve sizes involves a careful consideration of several critical factors:
-
Flow Rate: The primary determinant of gate valve sizes is the required flow rate of the fluid or gas passing through the system. A higher flow rate necessitates a larger valve to ensure adequate passage and minimize pressure drop.
- Calculating flow rate: Accurate flow rate calculations are crucial. Various methods can be employed, including measuring flow directly using flow meters, conducting hydraulic calculations based on system design parameters, or utilizing historical flow data.
- Flow velocity: The desired flow velocity within the pipe should also be considered. Excessive flow velocity can lead to erosion, cavitation, and other detrimental effects on the piping system.
-
Pressure Rating: Gate valves must be selected with a pressure rating that surpasses the maximum anticipated operating pressure within the system. This ensures the valve’s structural integrity and prevents potential leakage or failure.
- Pressure fluctuations: Consider potential pressure surges or fluctuations that may occur during system operation. The valve’s pressure rating should have a sufficient safety margin to accommodate these variations.
- Pressure testing: Valves are typically pressure tested during manufacturing to verify their ability to withstand specified pressures.
-
Material Compatibility: The choice of valve material is critical to ensure compatibility with the fluid or gas being handled.
- Corrosion resistance: The material must exhibit excellent resistance to corrosion from the fluid or gas, as well as any potential contaminants present in the system.
- Temperature resistance: The valve material must be able to withstand the expected temperature range of the application without significant degradation of its mechanical properties.
- Common materials: Common gate valve materials include carbon steel, stainless steel, cast iron, brass, and various alloys, each with its own specific advantages and limitations.
-
Temperature Range: The operating temperature range of the application significantly influences the selection of valve materials and their design.
- Extreme temperatures: Extreme temperatures, whether high or low, can affect the valve’s performance, potentially leading to thermal expansion, contraction, or embrittlement of the materials.
- Temperature variations: Consider potential temperature fluctuations within the system, such as those caused by seasonal changes or process variations.
-
Valve Type: Different types of gate valves exhibit varying size ranges and performance characteristics.
- Wedge gate valves: These valves feature a wedge-shaped gate that moves perpendicularly to the flow path, providing a tight seal when closed.
- Parallel disk gate valves: These valves employ two parallel disks that move together to block the flow. They are often preferred for applications involving abrasive fluids or slurries.
- Other types: Other types of gate valves, such as rising stem and non-rising stem valves, offer distinct advantages and should be considered based on specific application requirements.
Standard Gate Valve Sizes
Gate valves are available in a wide range of standard sizes to accommodate diverse piping systems and applications. Common standard sizes include:
- Small-diameter valves: 1/2 inch, 3/4 inch, 1 inch, 1 1/4 inch, 1 1/2 inch
- Medium-diameter valves: 2 inches, 3 inches, 4 inches
- Large-diameter valves: 6 inches, 8 inches, 10 inches, 12 inches, 14 inches, 16 inches, and larger
These sizes are typically based on industry standards and ensure compatibility with standard piping components. However, it’s important to note that manufacturers may offer custom sizes to meet specific project requirements.
Gate Valve Size Chart
The following table provides a general overview of common gate valve sizes and their corresponding nominal diameters. Please note that these dimensions may vary slightly depending on the specific valve design, manufacturer, and material.
NPS (in) | Nominal Diameter (in) | Approximate Weight (lbs) |
---|---|---|
1/2 | 0.540 | 0.5 |
3/4 | 0.824 | 1.0 |
1 | 1.050 | 1.5 |
2 | 2.067 | 4.0 |
3 | 3.068 | 10.0 |
4 | 4.026 | 18.0 |
6 | 6.065 | 45.0 |
8 | 8.075 | 90.0 |
10 | 10.020 | 150.0 |
12 | 12.090 | 250.0 |
How to Select the Right Gate Valve Sizes
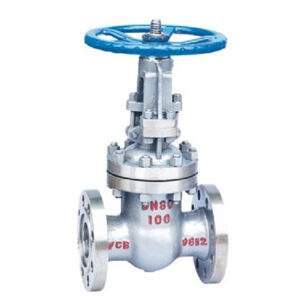
Selecting the appropriate gate valve sizes requires a systematic approach:
-
Determine the Flow Rate:
- Accurately calculate the required flow rate of the fluid or gas within the system.
- Utilize flow meters, hydraulic calculations, or historical flow data to obtain accurate flow rate values.
- Consider potential variations in flow rate due to changes in operating conditions or process demands.
-
Consider the Pressure Rating:
- Determine the maximum anticipated operating pressure within the system.
- Account for potential pressure surges or fluctuations.
- Select a gate valve with a pressure rating that significantly exceeds the maximum expected pressure to ensure safety and longevity.
-
Choose the Correct Material:
- Select a valve material that is highly resistant to corrosion from the fluid or gas being handled.
- Ensure the material can withstand the expected temperature range of the application without degradation.
- Consider factors such as abrasion resistance, chemical compatibility, and potential for stress corrosion cracking.
-
Specify the End Connections:
- Determine the appropriate type of end connections for the gate valve. Common options include:
- Threaded connections: Suitable for smaller valves and lower pressure applications.
- Flanged connections: Allow for easier installation, maintenance, and replacement.
- Welding neck flanges: Provide a strong, leak-tight connection for high-pressure applications.
- Butt-weld connections: Offer a seamless and robust connection for high-pressure and high-temperature applications.
- Determine the appropriate type of end connections for the gate valve. Common options include:
Conclusion
Selecting the correct gate valve sizes is a critical decision that significantly impacts the performance, reliability, and efficiency of your piping system. By carefully considering the factors discussed in this guide, including flow rate, pressure rating, material compatibility, and temperature limitations, you can make informed decisions to ensure optimal system operation and avoid potential problems.
Remember that consulting with a valve specialist is highly recommended for complex applications or when uncertainty exists regarding the best valve choice. By following these guidelines and seeking expert advice when necessary, you can confidently select the appropriate gate valve sizes for your specific needs and ensure the long-term success of your project.
FAQ
What is the most crucial factor in determining gate valve sizes?
Flow rate is the most crucial factor.
Can I use a larger gate valve size than what is theoretically required?
Generally, using a larger gate valve size than required is acceptable. However, it may lead to increased costs, higher pressure drop, and potential for excessive flow velocities.
When should I consult with a valve specialist?
Consult a valve specialist when unsure about the best gate valve sizes for your application, dealing with complex systems, or facing unique challenges like high pressures, corrosive fluids, or extreme temperatures.