Introduction
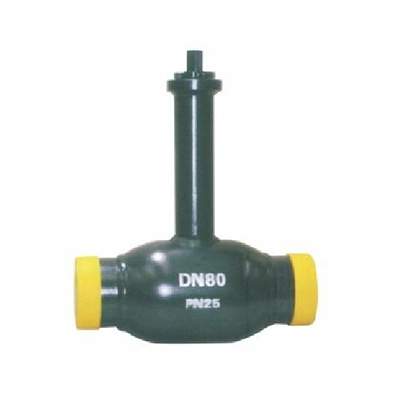
A gas ball valve is a type of quarter-turn valve that employs a spherical ball to regulate the flow of gas. This simple yet effective device is widely used in various industries due to its reliability, durability, and ease of operation. In this comprehensive guide, we will delve into the intricacies of gas ball valves, exploring their construction, working principle, advantages, selection criteria, and maintenance tips.
How Does a Gas Ball Valve Work?
At the core of a gas ball valve lies a spherical ball with a precise hole drilled through its center. This ball is meticulously fitted into the valve body and rotates on a stem. When the valve is in the open position, the hole in the ball aligns perfectly with the inlet and outlet ports, allowing gas to flow unimpeded. By rotating the stem a quarter-turn, the ball is positioned to obstruct the flow of gas, effectively shutting off the supply.
Advantages of Gas Ball Valves
Gas ball valves offer numerous advantages that make them a preferred choice for many applications:
- Quarter-turn operation: This design allows for swift and effortless on/off control, saving time and effort.
- Simple design: With fewer moving parts, gas ball valves are inherently reliable and less prone to mechanical failures.
- Tight shutoff: The spherical ball design ensures a tight seal, preventing gas leaks and maintaining system integrity.
- Bidirectional flow: Gas ball valves can handle flow in both directions, providing flexibility in various piping configurations.
- Variety of materials: Available in a wide range of materials, such as brass, stainless steel, and other alloys, gas ball valves can be tailored to specific applications and corrosive environments.
Construction of a Gas Ball Valve
A typical gas ball valve comprises the following essential components:
- Body: The main housing of the valve, providing structural support and enclosing the internal components.
- Ball: The spherical element with a precisely drilled hole, responsible for controlling the flow of gas.
- Stem: The rotating shaft that connects to the ball, enabling its rotation to open or close the valve.
- Seat: The sealing surface against which the ball presses to create a tight seal, preventing gas leakage.
- Actuator: The device used to rotate the stem, which can be manual (handwheel or lever), pneumatic, or electric, depending on the specific application requirements.
Types of Gas Ball Valves
Gas ball valves can be categorized based on various factors, including:
- Material: The valve body and internal components can be made of different materials, such as brass, stainless steel, or other alloys, to suit specific applications and environmental conditions.
- End connections: Gas ball valves are available with different end connections, including threaded, flanged, or welded, to ensure compatibility with various piping systems.
- Actuation: The valve can be actuated manually using a handwheel or lever, or it can be automated with pneumatic or electric actuators for remote control or integration into control systems.
- Temperature and pressure ratings: Gas ball valves are designed to handle specific temperature and pressure ranges, ensuring safe and reliable operation in diverse conditions.
Selection Criteria for Gas Ball Valves
When selecting a gas ball valve for a specific application, several factors must be carefully considered:
- Gas type and properties: The compatibility of the valve material with the gas being handled is crucial to prevent corrosion and ensure safe operation.
- Operating conditions: The temperature, pressure, and flow rate of the gas will influence the valve’s design and material selection.
- End connections: The valve’s end connections must match the piping system to ensure a secure and leak-tight installation.
- Actuation requirements: The desired level of automation, whether manual or automated, will determine the type of actuator needed.
- Safety considerations: In hazardous environments, safety-certified valves, such as explosion-proof or fire-safe models, may be required to mitigate risks.
Sizing a Gas Ball Valve
Proper sizing of a gas ball valve is essential to guarantee optimal performance and prevent damage to the valve. Key factors to consider during the sizing process include:
- Pipe size: The diameter of the pipe to which the valve will be connected directly impacts the valve’s size.
- Flow rate: The volume of gas that needs to pass through the valve per unit of time is a critical parameter.
- Pressure drop: The allowable pressure loss across the valve should be considered to avoid excessive energy loss.
Installation and Maintenance
Proper installation and regular maintenance are crucial to ensure the long-term performance and reliability of gas ball valves.
-
Installation:
- Ensure proper alignment of the valve with the piping system.
- Tighten connections according to the manufacturer’s specifications to prevent leaks.
- Verify the correct orientation of the valve to ensure proper flow direction.
-
Maintenance:
- Regularly inspect the valve for signs of wear, damage, or leaks.
- Lubricate the stem and packing gland as recommended by the manufacturer to reduce friction and prevent leaks.
- Perform periodic functional tests to verify the valve’s operation and sealing integrity.
- Clean the valve body and components to remove debris and prevent corrosion.
Common Applications of Gas Ball Valves
Gas ball valves find widespread application in numerous industries due to their reliability and versatility:
- Oil and gas: Controlling the flow of natural gas, petroleum products, and other fluids in pipelines and processing plants.
- Chemical processing: Handling corrosive and hazardous chemicals in various industrial processes.
- Power generation: Regulating the flow of steam and other fluids in power plants.
- Food and beverage: Used in sanitary applications to control the flow of gases and liquids in food processing and packaging.
Comparison of Gas Ball Valves vs. Other Valve Types
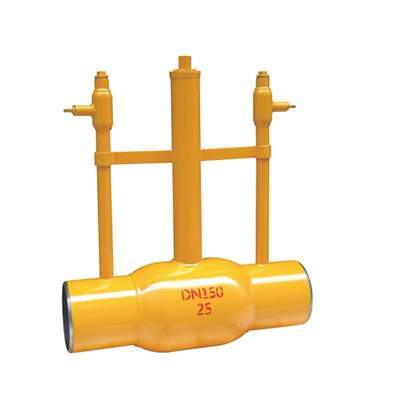
Feature | Gas Ball Valve | Gate Valve | Globe Valve |
---|---|---|---|
Quarter-turn operation | Yes | No | No |
Tight shutoff | Yes | Yes | Yes |
Flow control | Limited | Good | Good |
Pressure drop | Low | High | High |
Conclusion
Gas ball valves are versatile and reliable components that play a critical role in various industries. Their simple design, tight shutoff, and ease of operation make them a popular choice for controlling the flow of gases. By understanding the selection criteria, proper installation, and regular maintenance practices, you can ensure the long-term performance and safety of gas ball valves in your specific application.
FAQ
Q: What is the difference between a ball valve and a gate valve?
A: A ball valve uses a spherical ball to control flow, while a gate valve uses a wedge-shaped gate. Ball valves offer faster operation and tighter shutoff.
Q: How do I select the right material for a gas ball valve?
A: Consider the gas type, temperature, pressure, and corrosive environment. Common materials include brass, stainless steel, and other alloys.
Q: What is the purpose of a valve actuator?
A: A valve actuator provides the force or torque to open or close the valve, either manually or automatically.
Q: How often should I lubricate a gas ball valve?
A: The lubrication frequency depends on the valve’s usage and operating conditions. Refer to the manufacturer’s recommendations.