Introduction
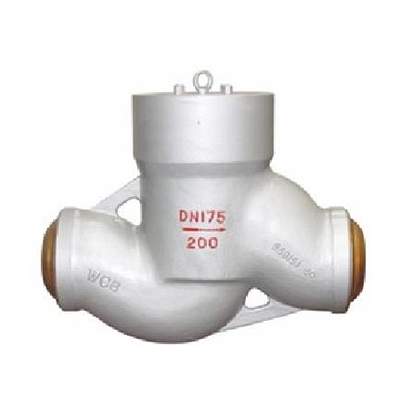
Power station check valves are indispensable components in the intricate network of power generation systems. These specialized valves play a pivotal role in ensuring the seamless and efficient operation of power plants by preventing the backflow of fluids. By safeguarding equipment and systems from potential damage, power station check valves contribute significantly to the overall reliability and longevity of power generation facilities. This comprehensive guide delves into the multifaceted world of power station check valves, exploring their diverse types, critical functions, essential selection criteria, meticulous installation procedures, and rigorous maintenance practices.
Understanding Power Station Check Valves
What is a Check Valve?
A check valve, a fundamental component in fluid dynamics, is a unidirectional flow control device. It ingeniously permits the fluid to flow in only one direction. When the fluid flow ceases or reverses, the valve instinctively closes, effectively preventing any backflow. This simple yet ingenious mechanism ensures that the fluid continues to flow in the intended direction, safeguarding the system from potential damage and operational disruptions.
Why are Power Station Check Valves Essential in Power Stations?
- Preventing Catastrophic Backflow: Power station check valves act as stalwart guardians, shielding pumps, turbines, and other critical equipment from the destructive force of backflow. By staunchly preventing the reversal of fluid flow, they mitigate the risk of equipment failure, operational downtime, and costly repairs.
- Preserving System Integrity: Power station check valves play a vital role in maintaining the integrity of the power station’s intricate system of pipes and valves. By ensuring unidirectional flow, they help to preserve system pressure and optimize overall efficiency.
- Enhancing Safety and Reliability: Power station check valves contribute significantly to the overall safety and reliability of power station operations. By preventing the accumulation of pressure in unintended areas, they mitigate the risk of hazardous conditions and accidents.
Types of Power Station Check Valves
Power station check valves come in a variety of designs, each tailored to specific applications and operational requirements. Some of the most common types include:
- Swing Check Valves: These valves feature a hinged disc that effortlessly swings open to allow forward flow and seamlessly closes to prevent backflow.
- Lift Check Valves: In lift check valves, a disc is ingeniously lifted off its seat to permit forward flow and gracefully drops back onto the seat to impede backflow.
- Ball Check Valves: A ball check valve employs a spherical ball as a flow control mechanism. The ball freely moves to allow forward flow and obstructs the passage to prevent backflow.
- Butterfly Check Valves: These valves utilize a disc that rotates to open and close, providing a compact and efficient design.
Selection Criteria for Power Station Check Valves
The selection of an appropriate check valve for a power station is a critical decision that requires careful consideration of various factors:
- Fluid Properties: The type of fluid being handled, including its physical properties such as viscosity, density, and corrosiveness, will significantly influence the choice of valve material and design.
- Operating Conditions: The prevailing operating conditions, including pressure, temperature, and flow rate, will determine the valve’s pressure class, temperature rating, and flow capacity.
- Cycle Life: The anticipated number of cycles and the valve’s durability are crucial considerations, especially in high-cycle applications.
- Material Compatibility: The valve material must be compatible with the fluid being handled to prevent corrosion, erosion, and other forms of material degradation.
Installation and Maintenance
The proper installation and maintenance of power station check valves are essential to ensure their optimal performance and longevity. Key considerations include:
- Piping Alignment: Meticulous attention must be paid to the alignment of the piping to avoid excessive stress on the valve and potential damage.
- Valve Orientation: The valve must be installed in the correct orientation to ensure unobstructed flow and efficient operation.
- Support Structure: Adequate support must be provided to the valve to prevent vibration, misalignment, and premature failure.
- Regular Inspection: Routine inspections are crucial to identify any signs of wear, damage, or leakage, enabling timely corrective actions.
- Periodic Testing: Regular testing of the valve’s functionality is essential to verify its performance and identify any potential issues.
Comparison of Check Valve Materials
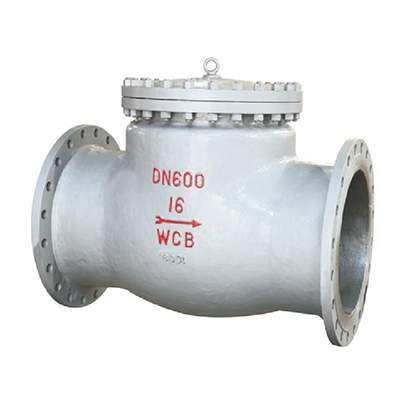
Material | Advantages | Disadvantages | Applications |
---|---|---|---|
Cast Iron | Cost-effective, good corrosion resistance | Heavy, limited temperature range | Low-pressure applications |
Stainless Steel | Excellent corrosion resistance, high strength | More expensive | High-temperature and corrosive applications |
Carbon Steel | Strong, durable | Susceptible to corrosion | General-purpose applications |
Conclusion
Power station check valves are indispensable components that play a pivotal role in ensuring the safe, reliable, and efficient operation of power generation facilities. By understanding the diverse types of check valves, meticulously considering selection criteria, and diligently adhering to installation and maintenance practices, engineers and operators can optimize the performance of their power plants and minimize the risk of costly disruptions.
FAQ
How often should check valves be inspected?
Check valves should be inspected regularly, typically as part of a preventive maintenance schedule. The frequency of inspection depends on factors such as operating conditions and fluid properties.
What are the signs of a failing check valve?
Signs of a failing check valve include excessive noise, vibration, leakage, or difficulty in opening or closing.
Can a check valve be repaired?
In some cases, check valves can be repaired, especially if the damage is minor. However, in many cases, it may be more cost-effective to replace the valve.
What is the difference between a check valve and a non-return valve?
Check valve and non-return valve are often used interchangeably, as they both serve the same purpose of preventing backflow. However, check valves are typically more robust and designed for higher-pressure and higher-temperature applications.