Introduction
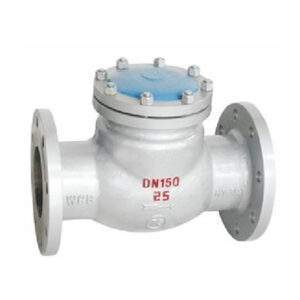
Straight stop valves, also known as in-line stop valves, are essential components in various piping systems, regulating the flow of liquids or gases. Their primary function is to completely shut off or allow flow, providing a reliable means of isolation for maintenance, repairs, or emergency situations. Unlike other valve types that offer throttling capabilities, straightstop valves are designed for on/off service, ensuring a tight seal when closed and minimal pressure drop when fully open. This blog post will delve into the intricacies of straight stop valves, covering their types, applications, selection criteria, and maintenance, helping you choose the right valve for your specific needs. Understanding the characteristics of a straight stop valve is crucial for ensuring the efficiency and safety of any fluid handling system.
Understanding the Different Types of Straight Stop Valves
Several types of stop valves cater to diverse applications and operating conditions. Each type has unique design features that determine its suitability for specific services. Some common types include:
Globe Valves as Stop Valves
Globe valves are a popular choice for stop valve applications, particularly when frequent operation is required. Their design features a spherical body with an internal baffle that creates a tortuous flow path. The disc, attached to a stem, moves perpendicular to the flow, closing against the seat to stop the flow. Globe valves offer excellent shut-off capabilities and can also be used for throttling, although they are primarily used for on/off service in many systems. The pressure drop across a globe valve is generally higher than that of other stop valve types.
Gate Valves as Stop Valves
Gate valves are another common type of stop valve, known for their minimal pressure drop when fully open. They operate by raising or lowering a gate-shaped disc within the valve body. When fully open, the gate is completely out of the flow path, offering virtually unobstructed flow. Gate valves are ideal for applications where infrequent operation is expected and a straight, unrestricted flow path is desired. However, they are not suitable for throttling service as partial opening can lead to erosion of the gate and seat.
Ball Valves as Stop Valves
Ball valves are characterized by a spherical ball with a bore through its center. Rotating the ball 90 degrees aligns the bore with the flow path, allowing flow, while rotating it another 90 degrees perpendicular to the flow path stops the flow. Ball valves offer quick on/off operation, tight shut-off, and minimal pressure drop when fully open. They are widely used in various applications due to their simplicity, reliability, and cost-effectiveness. The stop valve functionality of a ball valve is one of its most common uses.
Applications of Straight Stop Valves Across Industries
Straight stop valves find widespread use across various industries due to their essential function in controlling fluid flow. Some common applications include:
Straight Stop Valves in Water Treatment Plants
In water treatment plants, stop valves are used for isolating various sections of the treatment process for maintenance, repairs, or backwashing. They ensure that specific processes can be shut down without affecting the entire plant operation.
Stop Valves in Oil and Gas Pipelines
In the oil and gas industry, stop valves are critical for controlling the flow of hydrocarbons in pipelines. They are used for isolating sections of pipelines for maintenance, emergency shutdowns, or flow diversion.
Stop Valves in Chemical Processing Plants
Chemical processing plants utilize stop valves to control the flow of various chemicals throughout the production process. They are essential for isolating tanks, reactors, and other equipment for maintenance or process changes.
Straight Stop Valves in HVAC Systems
In heating, ventilation, and air conditioning (HVAC) systems, stop valves are used to control the flow of water or refrigerant in piping systems. They are used for balancing flow, isolating sections for maintenance, or shutting off flow to specific zones.
Key Factors to Consider When Choosing a Straight Stop Valve
Selecting the right stop valve is crucial for ensuring optimal performance and reliability of the piping system. Several factors should be considered during the selection process:
Material Compatibility of the Stop Valve
The valve material must be compatible with the fluid being handled to prevent corrosion, erosion, or other forms of material degradation. Common valve materials include brass, bronze, cast iron, steel, stainless steel, and various plastics.
Pressure and Temperature Ratings of the Straight Stop Valve
The valve must be rated for the operating pressure and temperature of the system. Exceeding these ratings can lead to valve failure and potential safety hazards.
End Connections of the Stop Valve
The valve end connections must be compatible with the piping system. Common end connections include threaded, flanged, and welded.
Valve Size and Flow Capacity of the Straight Stop Valve
The valve size should be selected to ensure adequate flow capacity without excessive pressure drop.
Actuation Method of the Stop Valve
Valves can be manually operated, or they can be actuated using pneumatic, electric, or hydraulic actuators. The actuation method should be chosen based on the application requirements.
Comparison of Straight Stop Valve Types
Feature | Globe Valve | Gate Valve | Ball Valve |
---|---|---|---|
Pressure Drop | High | Low | Very Low |
Shut-off Capability | Excellent | Good | Excellent |
Throttling Capability | Good | Not Recommended | Not Recommended |
Speed of Operation | Slow | Slow | Fast |
Cost | Moderate to High | Low to Moderate | Low to Moderate |
Maintenance | Moderate | Low | Low |
This table summarizes the key characteristics of different straight stop valve types, helping you to make an informed decision based on your specific application requirements. This comparison helps in understanding the nuances of choosing the correct straight stop valve.
Installation and Maintenance of Straight Stop Valves
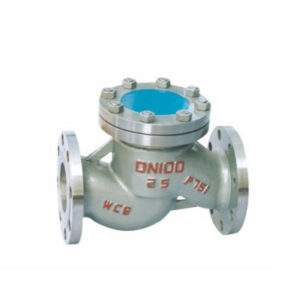
Proper installation and regular maintenance are essential for ensuring the long-term reliability and performance of straight stop valves.
Straight Stop Valve Installation Best Practices
- Ensure the valve is installed in the correct orientation according to the flow direction indicated on the valve body.
- Use appropriate sealing materials and techniques to prevent leaks.
- Support the piping system adequately to prevent stress on the valve.
Straight Stop Valve Maintenance Procedures
- Regularly inspect the valve for leaks, damage, or wear.
- Operate the valve periodically to prevent it from seizing.
- Lubricate moving parts as needed.
- Replace worn or damaged parts promptly. Regular maintenance of your straight stop valve is essential for ensuring its long-term reliability.
Conclusion
Choosing the right straight stop valve is critical for ensuring the efficient and safe operation of any fluid handling system. By understanding the different types of straight stop valves, their applications, selection criteria, installation procedures, and maintenance practices, you can make informed decisions and ensure the long-term reliability of your piping system. Remember to consider all relevant factors, such as material compatibility, pressure and temperature ratings, end connections, size, and actuation method, when selecting a straight stop valve. Regular maintenance is also essential for maximizing the lifespan and performance of these crucial components. A properly chosen and maintained straight stop valve is an investment in the efficiency and safety of your operations. This comprehensive guide should provide a solid foundation for understanding and selecting the appropriate straight stop valve for your needs. The straight stop valve remains a critical component in many industries, and proper selection is paramount.
FAQ
Can straight stop valves be used for throttling?
While some types, like globe valves, offer limited throttling capabilities, straight stop valves are primarily designed for on/off service.
How do I choose the right straight stop valve for my application?
Consider factors such as material compatibility, pressure and temperature ratings, end connections, size, and actuation method.
What is the difference between a globe valve and a gate valve?
Globe valves offer better shut-off and throttling capabilities but have higher pressure drop, while gate valves offer minimal pressure drop when fully open but are not suitable for throttling. The straight stop valve functionality is present in both but with different characteristics.
What are the advantages of using a ball valve as a straight stop valve?
Ball valves offer quick on/off operation, tight shut-off, minimal pressure drop, and are generally cost-effective. The straight stop valve characteristic of a ball valve is highly advantageous in many applications.