Introduction
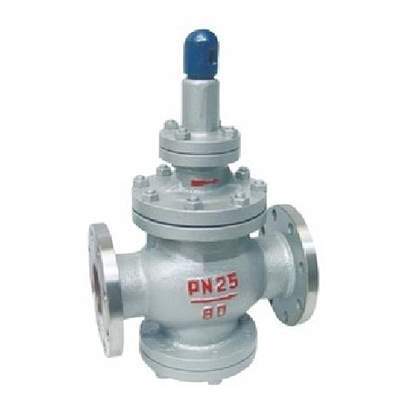
Hydraulic systems are integral to numerous industries, from manufacturing and construction to aerospace and agriculture. These systems rely on the power of pressurized fluid to transmit force and motion. At the heart of every efficient hydraulic system lies the crucial component: the hydraulic control valve. These valves are responsible for directing, regulating, and controlling the flow of hydraulic fluid, thereby governing the operation of the entire system. Understanding the benefits of using hydraulic control valves is essential for anyone working with or designing hydraulic systems. This blog post will delve into the various advantages these valves offer, exploring their functionalities and applications in detail. We will explore different types of hydraulic control valves and their specific benefits.
Precise Control with Hydraulic Control Valves
One of the primary benefits of hydraulic control valves is their ability to provide precise control over hydraulic systems. These valves offer exceptional accuracy in regulating fluid flow, pressure, and direction. This precision translates to several advantages:
- Accurate Positioning: Hydraulic control valves enable precise positioning of actuators, such as cylinders and motors. This is crucial in applications requiring fine movements, such as robotics, machining, and material handling. The precise control offered by hydraulic control valves ensures that movements are carried out with accuracy and repeatability.
- Smooth Operation: By controlling the flow of fluid, these valves ensure smooth acceleration and deceleration of hydraulic actuators. This prevents jerky movements and reduces wear and tear on the system components. Smooth operation is vital in applications where precision and stability are paramount.
- Variable Speed Control: Hydraulic control valves allow for variable speed control of hydraulic actuators. This means that the speed of the actuator can be adjusted as needed, providing flexibility in different applications. This adaptability is particularly useful in situations requiring varying speeds or force.
Enhancing Precision with Directional Control Valves
Directional control valves, a key type of hydraulic control valve, are specifically designed to control the direction of fluid flow within a hydraulic system. By selectively opening and closing internal passages, these valves direct the fluid to the desired actuator, enabling precise control over movement direction. This precision is essential in applications where accurate directional control is critical.
Increased Efficiency with Hydraulic Control Valves
Hydraulic control valves contribute significantly to the overall efficiency of hydraulic systems. Several factors contribute to this increased efficiency:
- Reduced Energy Loss: Efficiently designed hydraulic control valves minimize pressure drops and flow restrictions, reducing energy loss within the system. This translates to lower operating costs and reduced environmental impact. Minimizing energy loss is a key consideration in optimizing hydraulic system performance.
- Improved System Performance: By optimizing fluid flow and pressure, hydraulic control valves enhance the overall performance of the hydraulic system. This leads to faster cycle times, increased productivity, and improved overall efficiency. This optimization is crucial in demanding industrial applications.
- Optimized Power Transmission: Hydraulic control valves ensure efficient power transmission within the system by directing fluid flow to where it is needed most. This optimizes the use of available power and improves the overall efficiency of the system. Efficient power transmission is vital for maximizing system output.
Flow Control Valves and Efficiency
Flow control valves, another important type of hydraulic control valve, play a crucial role in enhancing system efficiency. These valves regulate the rate of fluid flow, ensuring optimal performance and minimizing energy waste. By precisely controlling flow rates, these valves contribute to overall system efficiency.
Enhanced Safety with Hydraulic Control Valves
Safety is paramount in any industrial setting, and hydraulic control valves play a vital role in ensuring the safe operation of hydraulic systems.
- Overload Protection: Many hydraulic control valves incorporate safety features such as pressure relief valves. These valves protect the system from overpressure conditions, preventing damage to components and ensuring safe operation. Overload protection is crucial for preventing accidents and ensuring system integrity.
- Controlled Deceleration: Hydraulic control valves enable controlled deceleration of hydraulic actuators, preventing sudden stops and reducing the risk of accidents. This controlled deceleration is particularly important in applications involving heavy loads or high speeds.
- Emergency Shut-Off: Some hydraulic control valves are designed for emergency shut-off, allowing for rapid system shutdown in case of an emergency. This feature is crucial for preventing further damage or injury in critical situations.
Pressure Control Valves and Safety
Pressure control valves are essential for maintaining safe operating pressures within a hydraulic system. These valves prevent overpressure and ensure that the system operates within safe limits. This is crucial for preventing accidents and ensuring the safety of personnel and equipment.
Versatility of Hydraulic Control Valves
Hydraulic control valves are incredibly versatile and can be used in a wide range of applications. This versatility stems from the wide variety of valve types and configurations available.
- Adaptability to Different Applications: Hydraulic control valves can be tailored to meet the specific requirements of different applications. This adaptability makes them suitable for use in various industries, from mobile equipment to industrial machinery.
- Wide Range of Sizes and Configurations: Hydraulic control valves are available in a wide range of sizes and configurations, allowing for integration into various hydraulic systems. This flexibility makes them suitable for both small and large-scale applications.
- Compatibility with Different Fluids: Hydraulic control valves are compatible with various hydraulic fluids, further enhancing their versatility and adaptability. This compatibility makes them suitable for use in diverse operating environments.
Directional, Flow, and Pressure Control Valves: A Versatile Trio
The three main types of hydraulic control valves – directional, flow, and pressure control valves – offer a wide range of functionalities, making them suitable for diverse applications. This versatility is a key advantage of using hydraulic control valves.
Durability and Reliability of Hydraulic Control Valves
Hydraulic control valves are designed for durability and reliability, ensuring long-lasting performance in demanding environments.
- Robust Construction: These valves are typically constructed from robust materials, such as steel and cast iron, ensuring resistance to wear, corrosion, and high pressures. This robust construction ensures long service life and reliable performance.
- Long Service Life: Properly maintained hydraulic control valves can provide a long service life, reducing downtime and maintenance costs. This longevity is a significant advantage in demanding industrial applications.
- Minimal Maintenance Requirements: While regular inspection is important, hydraulic control valves generally require minimal maintenance, further reducing operating costs and downtime.
Material Selection for Enhanced Durability
The materials used in the construction of hydraulic control valves play a crucial role in their durability and reliability. Selecting appropriate materials ensures resistance to wear, corrosion, and other environmental factors.
Cost-Effectiveness of Hydraulic Control Valves
While the initial investment in hydraulic control valves may seem significant, their long-term benefits contribute to overall cost-effectiveness.
- Reduced Downtime: The reliability and durability of hydraulic control valves minimize downtime, reducing production losses and associated costs.
- Lower Maintenance Costs: The minimal maintenance requirements of these valves contribute to lower operating costs over their lifespan.
- Improved System Efficiency: The increased efficiency offered by hydraulic control valves translates to lower energy consumption and reduced operating costs.
Long-Term Cost Savings
The long-term cost savings associated with reduced downtime, lower maintenance costs, and improved system efficiency make hydraulic control valves a cost-effective solution for many applications.
Types of Hydraulic Control Valves and Their Specific Benefits
Here’s a table summarizing the main types of hydraulic control valves and their key benefits:
Type of Hydraulic Control Valve | Key Benefits | Applications |
---|---|---|
Directional Control Valves | Controls the direction of fluid flow, enabling precise directional control of actuators. | Mobile hydraulics, industrial machinery, robotics. |
Flow Control Valves | Regulates the rate of fluid flow, ensuring optimal performance and minimizing energy waste. | Hydraulic presses, machine tools, injection molding machines. |
Pressure Control Valves | Controls system pressure, preventing overpressure and ensuring safe operation. Includes relief valves, reducing valves, etc. | Hydraulic power units, presses, clamping systems. |
Servo Valves | Provides highly precise and responsive control of fluid flow and pressure, used in closed-loop control systems. | Aerospace, robotics, testing equipment. |
Proportional Valves | Offers variable control of fluid flow and pressure, allowing for precise control of actuator speed and force. | Industrial automation, mobile equipment, material handling. |
Check Valves | Allows fluid flow in only one direction, preventing backflow and protecting system components. | Any hydraulic system needing one-way flow, such as pumps and accumulators. |
Spool Valves | Uses a spool to control fluid flow through internal passages, commonly used in directional control applications. | Mobile hydraulics, industrial machinery, agricultural equipment. |
Applications of Hydraulic Control Valves
Hydraulic control valves are used in a wide array of industries and applications, including:
- Manufacturing: Controlling machinery, robots, and automated systems.
- Construction: Operating heavy equipment such as excavators, cranes, and bulldozers.
- Agriculture: Powering tractors, harvesters, and other agricultural machinery.
- Aerospace: Controlling flight control surfaces, landing gear, and other aircraft systems.
- Material Handling: Operating forklifts, conveyors, and other material handling equipment.
- Automotive: Powering power steering, brakes, and other vehicle systems.
Troubleshooting Common Hydraulic Control Valve Problems
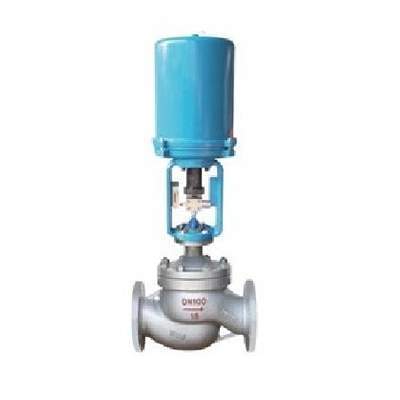
Even with proper maintenance, hydraulic control valves can sometimes experience problems. Here are some common issues and their potential causes:
- Leaks: Leaks can be caused by damaged seals, worn components, or loose connections. Identifying the source of the leak and replacing the affected components is crucial.
- Slow Response: Slow response can be caused by low fluid levels, contaminated fluid, or worn valve components. Checking fluid levels, filtering the fluid, and inspecting the valve can help identify the cause.
- Erratic Operation: Erratic operation can be caused by air in the system, worn valve components, or electrical problems. Bleeding the system, inspecting the valve, and checking electrical connections can help resolve the issue.
- Valve Sticking: Valve sticking can be caused by contamination, corrosion, or lack of lubrication. Cleaning the valve, ensuring proper lubrication, and addressing any corrosion issues can help prevent sticking.
- Excessive Noise: Unusual noise can indicate several problems, including cavitation, air in the system, or worn components. Addressing the root cause is essential to avoid further damage.
Conclusion
Hydraulic control valves are essential components in any hydraulic system, providing precise control, increased efficiency, enhanced safety, and versatility. Their durability, reliability, and cost-effectiveness make them a valuable investment for various industries. By understanding the benefits of using hydraulic control valves, you can optimize the performance of your hydraulic systems and achieve greater productivity and efficiency. From precise control of actuators to ensuring safe operation and optimizing energy efficiency, these valves play a crucial role in modern industrial applications. Choosing the right valve for the specific application and maintaining it properly are vital for maximizing its lifespan and performance.
FAQ
Q: What is the main function of a hydraulic control valve?
A: The main function of a hydraulic control valve is to direct, regulate, and control the flow of hydraulic fluid within a hydraulic system.
Q: What are the different types of hydraulic control valves?
A: The main types of hydraulic control valves are directional control valves, flow control valves, and pressure control valves. Other types include servo valves, proportional valves, check valves and spool valves.
Q: How do I choose the right hydraulic control valve for my application?
A: Several factors should be considered, including system requirements, application requirements, valve type, size, configuration, operating environment, cost, and availability.
Q: How do I maintain hydraulic control valves?
A: Regular inspections, fluid cleanliness, seal replacement, proper lubrication, and professional servicing are essential for maintaining hydraulic control valves.